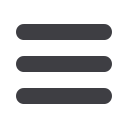
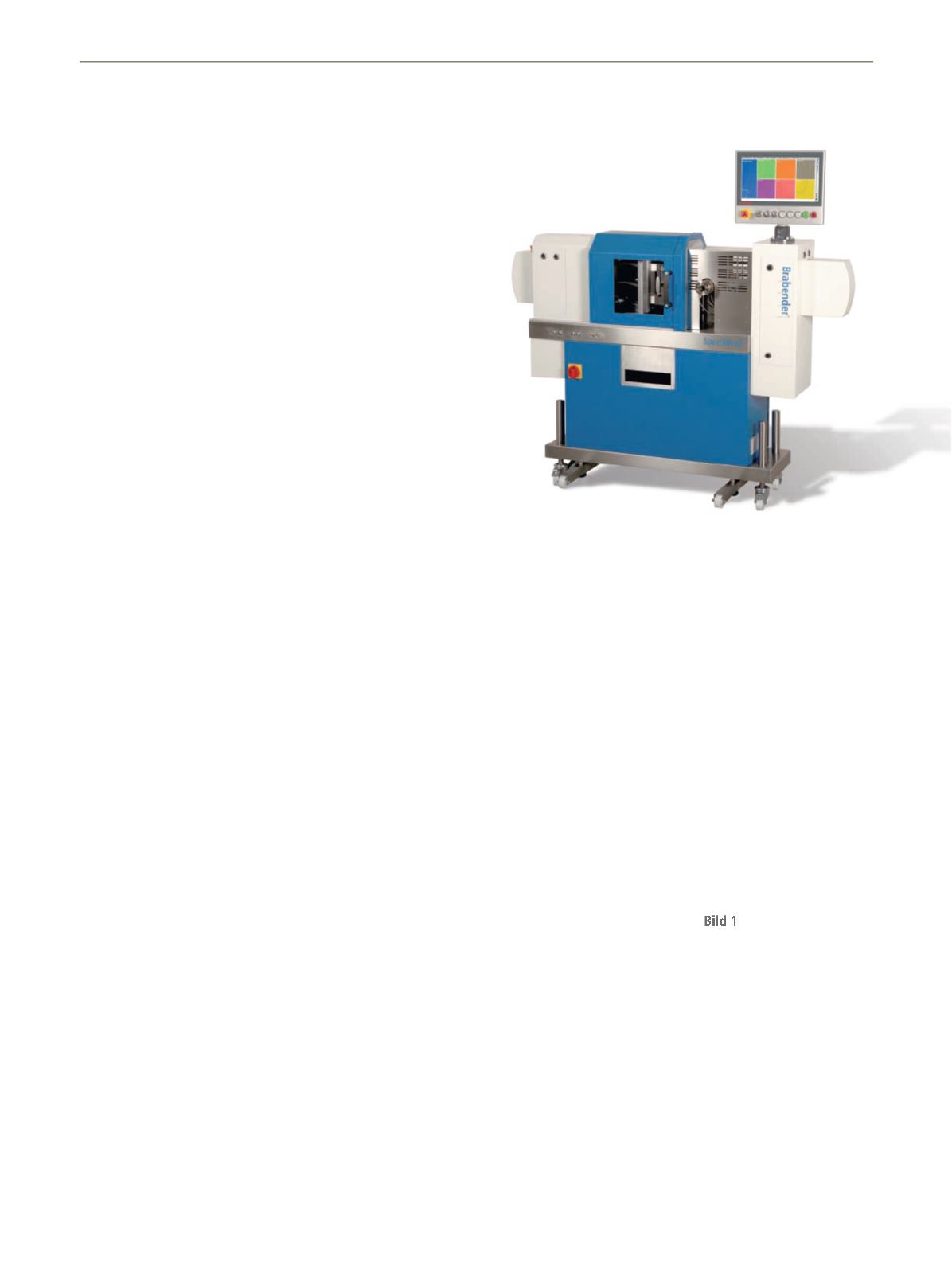
Michael Kunde, Brabender GmbH & Co. K
G
Eine neue Inline-Spritzgussmaschine für die schnelle
und energiesparende Prüfkörperherstellung kann
Compoundeure, Additivhersteller und Kunststoff-
Entwicklungslaboratorien dabei unterstützen, die
Kunststoff-Rezepturentwicklung zu beschleunigen –
und obendrein unverfälschte, praxisnähere Werkstoff-
kennwerte zu ermitteln. Das von der Brabender
GmbH & Co. KG unter dem Namen SpeciMold
vermarktete Aggregat wurde von den Duisburger
Polymeranalytik-Spezialisten gemeinsam mit dem
Fraunhofer-Institut für Umwelt-, Sicherheits- und
Energietechnik (UMSICHT) entwickelt. Es passt sich
nahtlos in bestehende Laboranlagen ein und löst auf
einen Schlag diverse Herausforderungen der
Compoundentwicklung, etwa im Blick auf die
Restfeuchte-Problematik oder den effektiven
Umgang mit geringen Materialmengen.
Inline-Probenkörper – ohne Granulie-
rung direkt aus dem Polymerstrom
:
Bei der Lösung dieses Zielkonflikts kann
den Entwickler in Zukunft eine neuartige
Inline-Spritzgussanlage für die Probe-
körperherstellung unterstützen: Der
SpeciMold, den die Brabender gemein-
sam mit dem Fraunhofer-Institut für
Umwelt-, Sicherheits- und Energietech-
nik (UMSICHT) entwickelt hat. In dieses
innovative Gerät bringt Brabender seine
jahrzehntelange Erfahrungen auf den
Gebieten der Extrusionstechnik und der
Prüfgeräte-Entwicklung für die Polymer-
branche ein (
).
Im „klassischen“ Workflow wird das
Materialmuster im Laborextruder granu-
liert und zum Spritzgießer geschickt, der
daraus Prüfkörper herstellt – ein zeitauf-
wendiger Prozess. Der SpeciMold dage-
gen fertigt spritzgegossene Probenkör-
per für eine Vielzahl gängiger Laborun-
tersuchungen bereits aus dem zur Gra-
nulierung bestimmten Polymermuster –
und zwar schnell und inline, also direkt
aus dem extrudierten Polymerstrom.
Zweiter Vorteil: Mit dem SpeciMold produ-
zierte Probenkörper entsprechen dem End-
produkt in Bezug auf zentrale physikali-
sche Kennwerte besser als solche, die im
P
olymere Werkstoffe haben sich in den
vergangenen Jahrzehnten zu immer
wichtigeren Stützen unseres Alltags ent-
wickelt. Dabei schieben die Anwender
vormals bestehende Leistungsgrenzen
immer weiter hinaus – zum einen durch
bemerkenswerte werkstoffliche bzw.
prozesstechnische Neuentwicklungen,
zum anderen durch immer smartere
Compoundierung. Polyamide zum Bei-
spiel, die unter anderem dank eines
hohen Glasfaseranteils und speziellen
Stabilisierungssystemen bis zu deutlich
über 200 °C wärmealterungsbeständig
sind, hätten noch vor wenigen Jahren als
Sensation gegolten. Erfolgsmeldungen
wie diese dürfen aber nicht den Blick
darauf verstellen, dass man sich mit der-
artigen Kunststoffen immer auf anwen-
dungstechnisches Neuland begibt, nicht
selten sogar an die Grenze des technisch
Machbaren. Um so wichtiger ist daher
eine versierte Analytik, die die Labormus-
ter teurer neuer Compounds im Zuge der
modernen Rezepturentwicklung auf
Herz und Nieren prüft – auch wenn diese
lediglich in Kleinstmengen vorliegen.
Compoundentwicklung ist zu einer
zeitkritischen Aufgabe geworden
:
Es
ist eine große Kunst, den Verarbeitungs-
40
Compoundieren
Extrusion 1/2017
Bild 1: „Zeitmaschine“ aus Duisburg: Der SpeciMold,
eine innovative inline-Spritzgussmaschine von Brabender
kann helfen, Entwicklungsprozesse in der Polymerbranche
deutlich zu verkürzen
prozess beim Spritzgießer schon im
Labor so detailliert wie möglich abzubil-
den. Nur so ist jedoch sichergestellt, dass
das vielversprechende Material aus dem
Technikum auch im spritzgegossenen
Endprodukt das hält, was es laut Daten-
blatt verspricht. So sollte zum Beispiel die
Zudosierung von flüssigen oder festen
Rezepturkomponenten im Laborextruder
so praxisnah wie möglich erfolgen.
Dabei spielt allerdings der Parameter Zeit
eine immer wichtigere Rolle, denn die
Werkstoffentwicklung steht immer öfter
unter erheblichem Zeitdruck. Um Pro-
dukte mit einem maßgeschneiderten
Eigenschaftsprofil zu erhalten und die
Potenziale polymerer Werkstoffe wirklich
auszureizen, werden Kunststoffanbieter
bzw. Compoundeure optimalerweise
immer früher in den Entwicklungspro-
zess eingebunden. Damit stehen sie aber
auch vor der Aufgabe, sich an die enorm
beschleunigten Innovationszyklen anpas-
sen zu müssen: Die Entscheidung für
oder gegen einen Werkstoff fällt in aller
Regel sehr früh, entsprechend schnell
müssen die Kunststoffanbieter ihren
Kunden eine zuverlässige Lösung präsen-
tieren, obwohl die Werkstoffentwicklung
immer komplexer wird.
Schneller zum Prüfling!
Kunststoff-Rezepturentwicklung beschleunigt