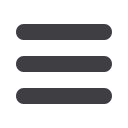
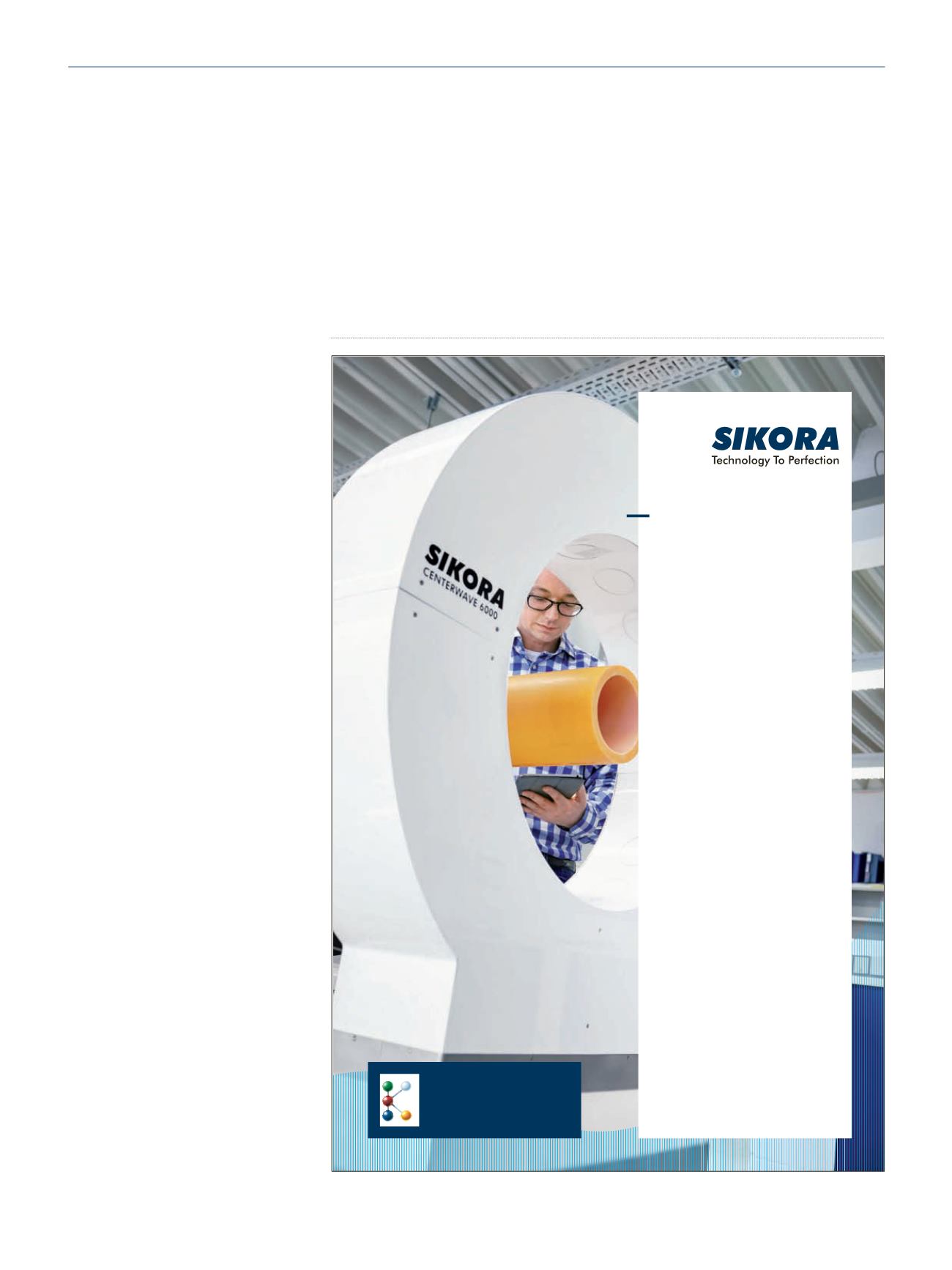
Quality in its
innovative
form.
With passion, we develop future-
oriented measuring and control
devices for quality assurance of
hoses and tubes, such as the
CENTERWAVE 6000
. A non-con-
tact system for the measurement
of diameter, ovality, wall thickness
and sagging of large plastic tubes
with a diameter from 120 to 2,500
mm. An innovative solution based
on millimeter wave technology
that increases product quality and
HQVXUHV VLJQLÀFDQW PDWHULDO DQG
cost savings during extrusion.
– easy operation without pre-
setting product parameters
– measurements independent from
material and temperature
– measuring results in real time
available for display and control
– reliable without calibration
www.sikora.net/centerwave6000Visit us from October 19-26
at the K 2016 in Düsseldorf,
Germany.
Hall 10, Booth H21
cannot be distorted during trans-
mission. The temperature sensors
delivery digital values with a preci-
sion of ± 0.5 degrees C, (upon re-
quest, als up to ± 0,1 degree C )
across a range of 100 degrees C.
“Derichs consciously selected a wi-
reless, digital date transmission me-
thod” explains Professor Kueng
“because the sensors are on the ro-
tating roller and cables in the vici-
nity of moving machine parts are
obstructive. It was important that
the data transmission be secure
and, upon request, encrypted and
that the radio protocol is standardi-
zed. The radio protocol meets the
Bluetooth 4.0 standard. Every mo-
dule has its own address so diffe-
rent sensors can clearly be assigned
to the measurement point and ma-
chine. Every five seconds, each mo-
dule is queried and these values can
also be tracked in live view mode
on an iPad tablet (Android in plan-
ning) or on a PC using a wireless
dongle.” The module can also log
values autonomously. The time in-
terval can be selected. The history
log files can be targetedly collected,
saved on the system side and eva-
luated, either manually or automa-
tically.. “It is a very valuable tool for
process engineers,” says Professor
Keung. "The module works in an
industrial temperature range of -40
to +85 degrees C. If thermally insu-
lated, the sensors can also be used
in rollers at up to 400 degrees C. “If
the process computer is connected
to the Intranet or Internet, this data
can be queried from anywhere.
“Thus Derichs has taken the first
big step toward the IoT: less waste,
less energy consumption, fewer
down-times.”
Passion for precision:
The name Derichs is known world-
wide for high-precision rollers in the
plastics industry and have always
stood for innovation and develop-
ment. With the Derichs ED1, the
new company management under
a female leadership (Maria Barthels
and Stephanie Holzmann) also pro-
➠ www.derichs-gmbh.deExtrusion International 5/2016
37
ves that it stands for quality and competence. Curious about the requirements of the
future, solution-oriented and innovative with respect to development, the DERICHS
ED1 is another milestone in the history of the plastics industry.
Right on time for the “K”:
This new development (including the shuttle) will be introduced for the K 2016 at an
exclusive in-house presentation on October 20th, at Derichs in Krefeld. Guest spea-
kers, including speakers from the ZHAW (Zürcher Hochschule für Angewandte Wis-
senschaft, School of Engineering, ZSN) will also be present.