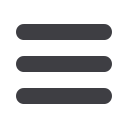
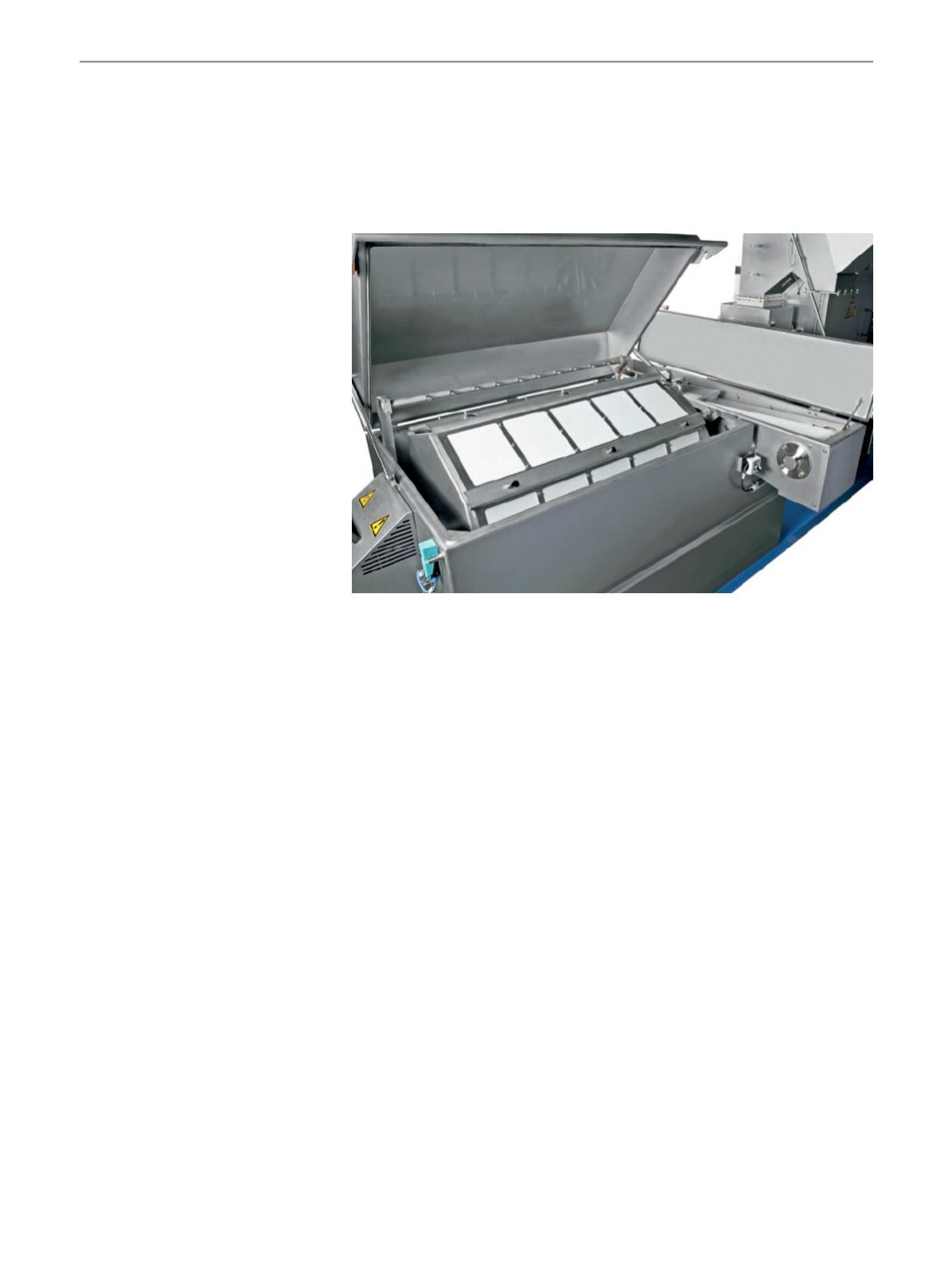
Portfolio of Pelletizers has Systems for
every Type of Operation
By Frank Asmuss,
global product manager,
BKG
®
pelletizing systems,
Nordson Corporation
There exists a vast potential for
pelletizing systems, driven by
strong global growth in con-
sumption of plastic products and
a gathering trend toward meet-
ing this demand through loca-
lized polymer production. In
countries where plastics con-
sumption is growing most
rapidly, more and more raw
materials for plastic products
will come from domestic resin
manufacturers, compounders,
and recyclers.
A
s the leading supplier of underwater pelletizing systems,
Nordson Corporation is prepared to meet the full range of
requirements that the huge and diversified global market can
be expected to present. These may range from basic systems
calling for minimal investment, to sophisticated and automated
production lines, to fully engineered turnkey operations for
high-volume producers serving multinational markets. Nord-
son’s BKG
®
range of underwater pelletizing systems has a
tiered structure, with different types of equipment available for
different levels of cost and sophistication.
In addition to a comprehensive portfolio of underwater pelletiz-
ing systems, Nordson offers related melt processing compo-
nents as part of its Nordson Polymer Processing Systems (PPS)
family of brands. These include Xaloy
®
screws and barrels for
extrusion and injection molding lines, BKG
®
melt filtration sys-
tems, melt pumps and polymer valves. Working with plastic
producers and extrusion machinery OEMs, Nordson is prepared
to recommend and design fully integrated underwater pelletiz-
ing production operations.
Underwater pelletizing: how it works
In underwater pelletizing, molten thermoplastic is extruded or
pumped through a die body containing holes arranged in a cir-
cular pattern. The downstream die face is completely encapsu-
lated in water, and as the molten material exits the die holes, it
is immediately cut by a rotating cutter and quenched by the
flowing water. The molten material solidifies, taking the shape
of a sphere to minimize surface tension, thus creating a round
pellet. These round pellets are then transported by water flow
away from the cutting chamber and into a secondary step
28
Polymer Processing
Extrusion 4/2017
Polygon Filter & Water Tank
(Images: Nordson)
where water and pellets are separated, most commonly by
means of a centrifugal dryer. After exiting the dryer, the round
pellets generally have very little surface moisture and are ready
to be packaged in a container or transported to another pro-
cess, if applicable.
A consistent melt pressure is critical to maintaining a uniform
pellet shape as well as avoiding freeze-off of the polymer in the
die holes. In order to ensure the necessary constant melt pres-
sure, Nordson can supply a BKG
®
melt pump that rotates at a
constant speed, metering a constant volume of polymer. This is
an example of how customers benefit from the depth of pro-
duct offerings within the Nordson PPS portfolio.
One advantage of underwater pelletizing over the alternative
method of strand pelletizing is that it can be used with materi-
als over a wide range of viscosities, whereas very low-viscosity
materials cannot form a strand, and highly filled materials cre-
ate fragile strands. In fact, underwater pelletizing can be used
not only for all thermoplastic polymers but also materials which
behave like thermoplastics. Some examples include: polyole-
fins, styrenics, PET, polyamides, PMMA, polycarbonate, TPEs
and TPU’s, hot-melt adhesives, natural resins (e.g. chewing
gum), PVC, and synthetic resins (e.g. epoxy resin).
The spherical pellets formed in underwater pelletizing flow bet-
ter than the cylindrical pellets created in strand pelletizing, re-
melt with less energy, and package more densely. All three dif-
ferences result in energy savings in comparison with strand pel-
letizing. In addition, underwater pelletizing systems are more
compact, and because they are totally enclosed systems, no
dust or vapor emissions take place.