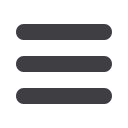
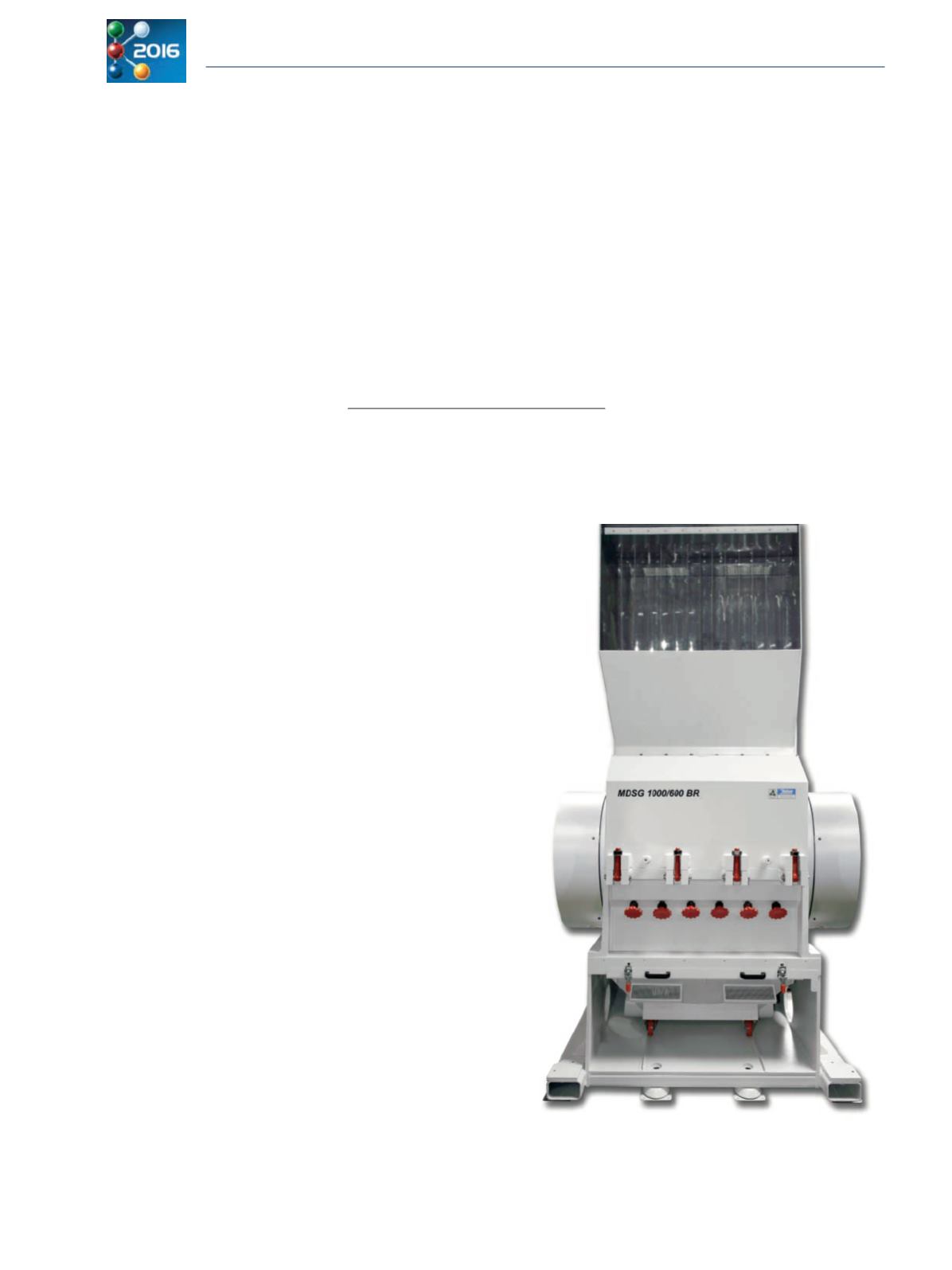
H
ellweg Maschinenbau GmbH & Co. KG presents at K 2016 its
new high performance granulator MDSG 1000/600 BR (“BR”
stands for “Brocken”, the German word for lumps), which works on
the peeling cutting principle and has been constructed for single-
stage shredding and granulation of solid start-up blocks and pipes &
sheets.
The machine has been designed as a robust welded construction and
is fitted with a solid peeling cutting action rotor. It is able to process,
in a single stage, heavy start-up lumps as well as pipes and sheets in
wall thicknesses of, for example, 500 mm into granulate characteri-
sed by its homogeneity and freedom from dust.
The geometry of the blades used enables a cutting principle known
as the so-called “peeling cut”, combined with limitation of cutting
depth, This prevents the rotor blades from cutting too deep into the
plastic material to be granulated. Material is simply “peeled off” from
lumps, as this prevents rotor blockage and guarantees fast, quiet and
energy saving shredding and granulation. With 1,000 mm working
width, the 12-bade U-CUT rotor has 600 mm diameter and it can be
sharpened a number of times by regrinding. The rotor is produced
from a single solid piece of steel and weighs approx. 4,000 kg. The
overall weight of the machine amounts to approx. 11,000 kg.
Depending on the material to be granulated, achievable throughput
ranges amount to between 800 and 3,000 kg/h, allowing for 5-20
mm diameter sieve perforation and 75-90 kW installed power rating.
Complete noise protection cabins as well as feeding equipment for
sheets and pipes are available as options.
MDSG 1000/600 BR lump granulator
Hellweg Maschinenbau:
new high
performance granulator
Hall 11, Booth B39
➠ www.schneidmuehlen.desation) exceeds the security-levels required in the food packa-
ging industry. This process design already incorporates high
decontamination performance and therefore opens the flexi-
ble usage of rPET for any kind of application – food or non-
food.
S.M.A.R.T. DIALOG –
Decontamination Performance – Quality Assured
.
S.M.A.R.T. DIALOG is a system, which allows the machine self-
monitoring, data can be recorded and analyzed – easily ac-
cessible on any device. For Food Grade applications, the
decontamination performance is automatically monitored and
the data is logged. A recipe-management on the equipment
allows for PET input material to be classified and also logged
together with production-data – traceability included.
(S.M.A.R.T. = Self-Monitoring Analysis + Reporting Techno-
logy).
The LSP process (Liquid State Polycondensation) has been in-
troduced at the K2013. The according machine series P:REACT
is operational at fiber-manufacturers, carpet-producers and
food-contact sheets and trays recyclers, in Europe and the
USA.
Hall 16, Booth A43
➠ www.ngr.atExtrusion International 5/2016
66