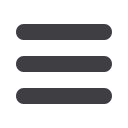
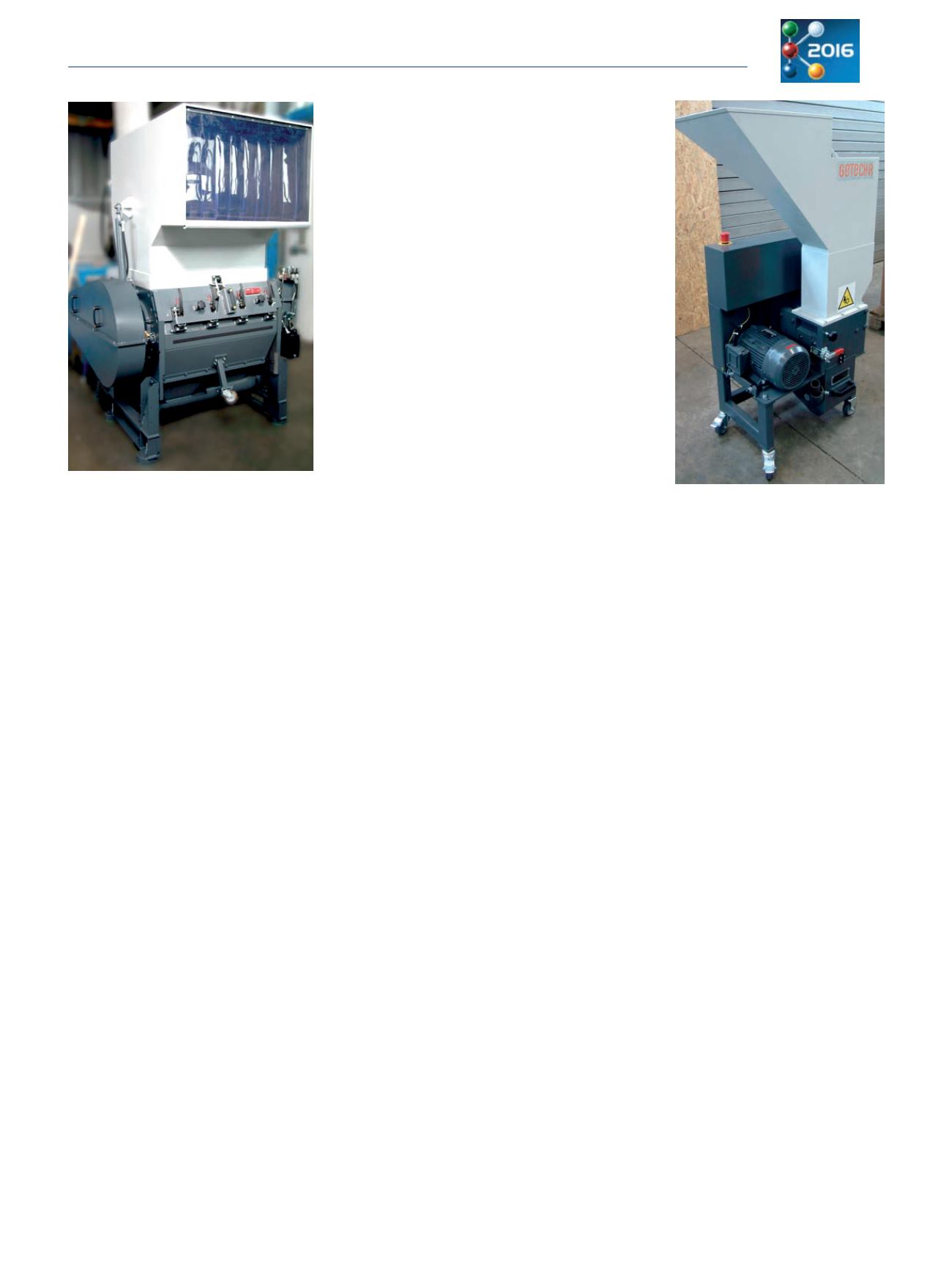
trusion as well as
with another bypass
hopper at the rear
for the plate mate-
rial feed. In this ver-
sion, the RS 45090
from Getecha can
be fed from three
sides (front, side,
rear). For the user
this means that at
best he will only
need one granulator
instead of three! An
important basis for
the realisation of
these optimisations
is, in addition to the
high overall stability
of the granulator, its
powerful 3-blade
rotor and the usage
of two stator blades
in the milling device.
Last but not least,
the RS 45090 from
Getecha will delight
maintenance engineers with an electrohydraulic opening me-
chanism, which simplifies access to the hopper and the screen
rocker.
Torque control instead of floating roller control system
Getecha will present another technical highlight at the K in
Düsseldorf (19 - 26 October 2016) with its new torque con-
trolled infeed system based on the example of another sound-
insulated infeed granulator RS 3004-E. This granulator type is
fundamentally designed for usage in film and plate extrusion
and has a double infeed system, with which offcuts and edge
trims of different thicknesses can be fed at different speeds. A
floating roller control system with dancer arm has proven itself
for many years for this purpose, synchronising the speed of
the edge trim feed with the speed of the film system and con-
trolling the tensile load of the edge trims. However, the edge
trim granulators are to be parked more and more frequently
very close to the extrusion line, where many machines com-
pete for a footprint. For this reason, Getecha has developed a
new, much more compact solution: The maximum torque of
the infeed drive is now configured via a parameter of the fre-
quency converter, thus optimising the traction on the edge
trim as well as the infeed speed. This saves a lot of space and
renders the mechanical floating roller control system with
dancer superfluous. How smoothly this works in practice, visi-
tors of the K will be able to see for themselves at the Getecha
booth in hall 3.
Getecha will be showing off its dustproof clean room slider
granulator GRS 180 in Düsseldorf as granulation solution for
production lines of pla-
stics technology with in-
creased demands on
hygiene and cleanliness. It
works with a scissor-cut
rotor and is designed for
hourly throughput rates
of up to 35 kg. However,
the GRS 180 scores parti-
cularly high with an auto-
matic lock hopper, an
integrated extraction con-
tainer and numerous
measures relevant for sealing. The result: This granulator lets
very few dust particles or ground material escape into the en-
vironment, and thus corresponds to the clean room demands
(particles <1.0 µm) of many plastic processors.
Optimising preparation processes
This year's K exhibition program from Getecha will be rounded
off by the compact RS 1615 and the sprue picker GETpick 700.
The RS 1615 is a very slim beside-the-press granulator for
hourly throughput rates of up to 25 kg. It is a proven solution
for decentralised use and has been continuously further de-
veloped in past years – most of all with regard to simplified
operation and maintenance. The GETpick 700 on the other
hand represents an example of the broad Getecha range of
sprue pickers and extraction systems with which material cy-
cles and preparation processes can be optimised with regard
to handling. The GETpick 700 is regarded as very popular – as
it is very reasonably priced – entry-level version. Its elegant li-
near technical design is intended for sprue weights of up to
250 g, operates in Y-direction with a light carbon fibre tube
and has three permanently programmed operating programs.
The extraction stroke is 500 or 700 mm and the extraction
cycle is less than 1.5 sec.
Whether it is extrusion technology, thermoforming, blow
moulding technology or injection moulding technology – at
this year's K booth of Getecha in hall 9, plastics processors of
all disciplines can not only familiarise themselves with the gra-
nulation-related system solutions of the plant construction
company, but also with the company's now very comprehen-
sive automation portfolio. It ranges from project planning and
development, engineering, programming and assembly to
commissioning, maintenance and service.
Such a hopper granulator of type RS
45090 will be shown by Getecha at the K
in hall 9 with a sound-insulated
granulator housing as well as with
additional bypass hoppers on the side
and at the rear panel for feeding tubing,
profiles and plate material
This year's K exhibition
program from Getecha also
includes the compact RS
1615, which was
developed for hourly
throughput rates
of up to 25 kg
Hall 9, Booth A21
➠ www.getecha.deExtrusion International 5/2016
63