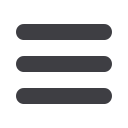
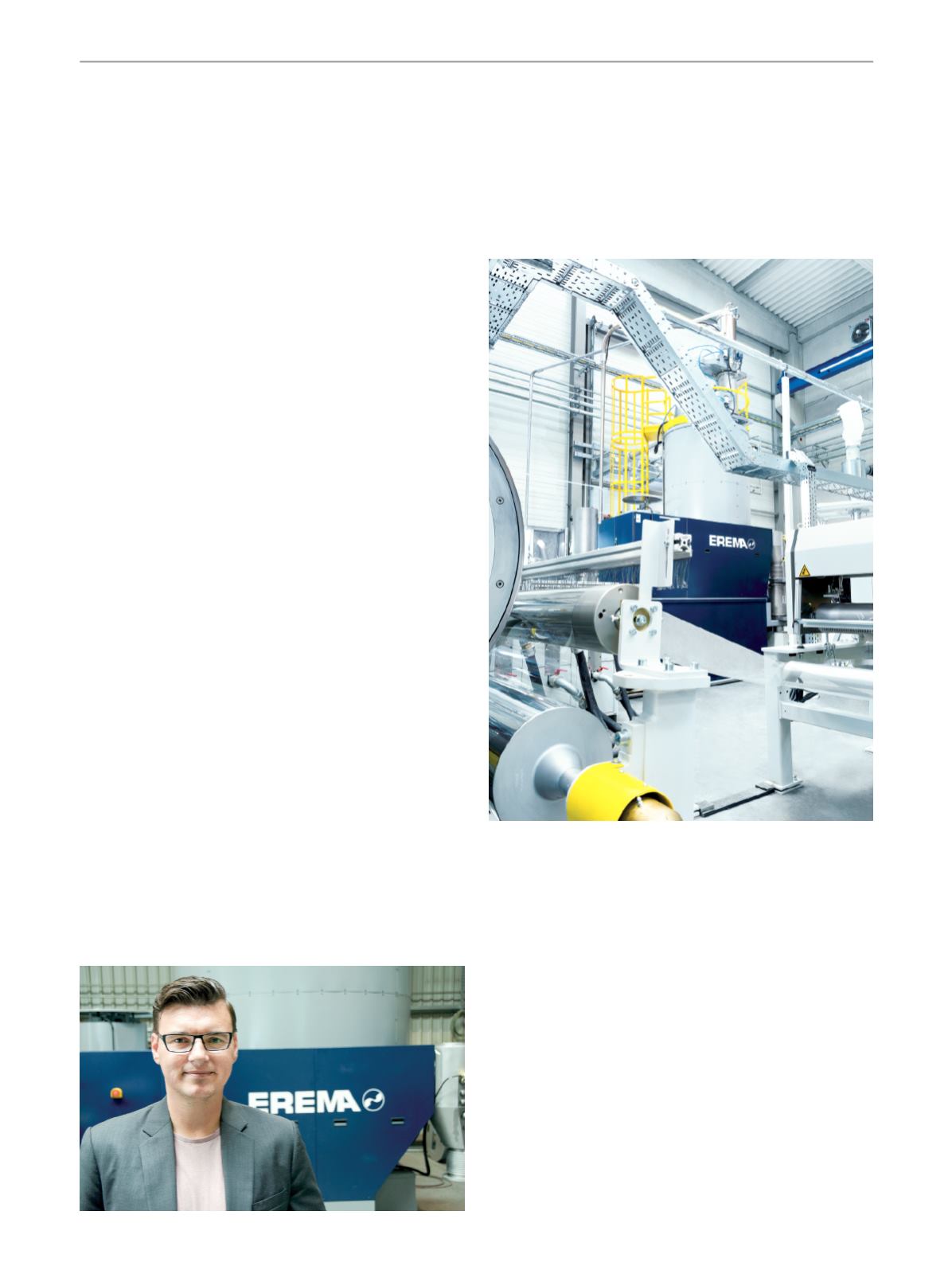
W
eltweit werden bereits jährlich 1,3 Mio. Tonnen PET mit
der VACUREMA Technologie von EREMA recycelt. End-
produkte sind unter anderem lebensmittelechte Preforms für
die Getränkeindustrie, Tiefziehfolien, Fasern oder Umreifungs-
bänder.
Die Auftragszahlen bei EREMA belegen, dass der Trend im PET-
Recycling deutlich in Richtung Direkt-Verarbeitung geht. Dabei
entfällt die Granulatproduktion als Zwischenschritt und Post
Consumer PET Flakes oder auch PET Produktionsabfälle werden
direkt und in einer Wärme zu Endprodukten verarbeitet. Alleine
in den letzten 15 Monaten wurden 24 dieser VACUREMA Inline
Anlagen ausgeliefert und zusätzlich ein neues Verfahren für die
direkte Produktion von lebensmittechten Preforms aus Post
Consumer Bottle Flakes präsentiert.
Für Kunden, die ihre bereits bestehende PET-Extrusionsanlagen
für lebensmitteltaugliche Endprodukte umrüsten, bietet EREMA
zusätzlich den MPR, einen hocheffizienten Kristallisationstrock-
ner. Dekontamination, Trocknung, Entstaubung und Kristallisati-
on von unterschiedlichen PET Inputmaterialien erfolgen vorbe-
reitend für die Extrusion in nur einem Schritt.
„Der MPR ist mehr und mehr bei Kunden gefragt, die einen
herkömmlichen Kristallisierer und Vortrockner haben, und mit
langer Prozesszeit und hohen Betriebskosten konfrontiert sind.
Mit einem Energieverbrauch von nur 0,1 kWh/kg ist der MPR
Energiesparende Add-On-Technologie –
Lebensmitteltauglichkeit inklusive
Vor einem Jahr gab EREMA am Discovery
Day den Relaunch des Multi Purpose Reac-
tor, kurz MPR, bekannt. Der Trend hin zu
lebensmittelechter Direkt-Verarbeitung
von PET-Produkten hat sich seither weiter
verstärkt. Immer mehr Kunden ergänzen
ihre bestehende Extrusionsanlage um das
Attribut der Lebensmitteltauglichkeit.
28
Recycling
Extrusion 6/2017
Alles in einem Arbeitsschritt: Das Inputmaterial gelangt
vom MPR in das Extrusionssystem und wird im Anschluss
direkt zu einem Inline Sheet Produkt
verarbeitet
Christoph Wöss vor dem MPR von Sky-Light in der
Produktionshalle von EREMA
Kristallisierer und Vortrockner zugleich und somit die wirt-
schaftlich interessantere Alternative“, betont Christoph Wöss,
Business Development Manager für den Bereich Bottle bei
EREMA. Inputmaterialien wie gewaschene PET-Bottle-Flakes,
gemahlene PET-Flachfolienabfälle als auch PET-Neuware sowie
deren Mischungen werden dekontaminiert und so bereits vor
der Extrusion lebenmitteltauglich. „Die Liste von Alternativan-
bietern diverser PET-Extruder ohne Vorbehandlung ist lange
und verlockend. Aber nachträgliche Investitionen für Trockner
oder wartungsintensive Dekontaminierungsmodule verringern
am Ende die Profite der PET-Produzenten“, warnt Wöss.