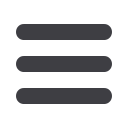
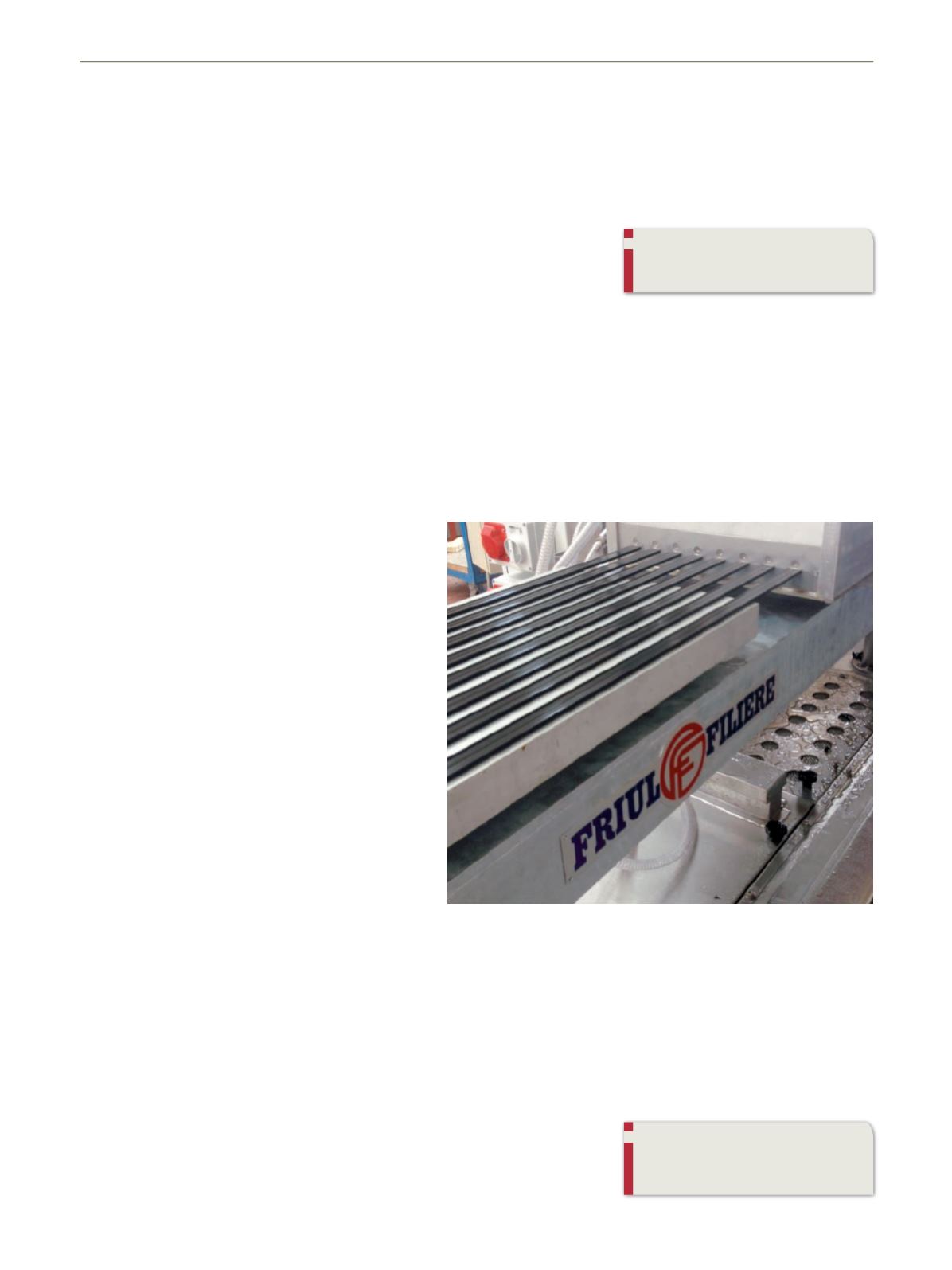
33
Extrusion 3/2016
Greiner Extrusion GmbH
office@greiner-extrusion.at www.greiner-extrusion.attrusion. The joined-in gaskets can be ex-
changed and easily recycled. The joined-
on gaskets stand out through optimum
adhesion. Two variants of joined-on gas-
kets can be processed during RED.PCE
production: firstly, with the well-known
heated-air function and secondly, using
the recently developed variant with the
pre-heater rail. With the heated-air va-
riant the welding area is heated with an
air jet. For this purpose, additional equip-
ment is required such as the heat exten-
sion, leister hot air blower, and control
box.
The second variant with the contactless
pre-heater rail is called RED.PCE plus.
With the RED.PCE plus system the join-
ing surface of the carrier profile is heated
with the pre-heater rail and the welding
surface is extended with an additional
blade. After this, the gasket is directly
joined onto the carrier profile. This pro-
duction process distinguishes itself
through optimum adhesion and exact
positioning to the profile.
Friul Filiere SpA has realized for a
European customer a Turn-Key project
for the extrusion of thermal break pro-
files in eight strands. An excellent
result considering the particular cha-
racteristics of this material. PA66 25%
GF is a nylon (in this case reinforced
with 25-30% of fiber glass) with very
high processing temperatures which
entail calibration difficulties. Further-
more, the reduced tolerances (in the
order of hundredths) which requires
their application within windows and
the production of eight profiles simul-
taneously, further complicate the
extrusion process.
T
he plant ensures the production of
eight profiles at 2 mt/min (90 kg/h)
and it is composed of a single-screw ex-
truder Omega80 with PLC, in which the
raw material arrives already dried, and
classical downstream with insertion of
auxiliary machines. A gear pump helps
the process stability but the material
flow is constant and homogeneous,
despite the complexity of the eight
strands, thanks to the special technolo-
gy Friul Filiere applied to the die. Fur-
thermore Friul Filiere’s calibration tech-
nology is able to work easily without
any need of intensive cooling devices.
The control of the eight strands is as-
sured by a dedicated calibration system
with die-calibrator centering which al-
lows a perfect alignment and facilitates
the positioning of the profiles.
The flexibility of the extrusion plant has
allowed the insertion in line of a sand-
blasting unit and a glue insertion sys-
tem. The sandblasting unit prepares the
profile surface that will be varnished to-
gether with the window frame, allow-
Complete Extrusion Plant for the
Production of Thermal Break Profiles
Friul Filiere SpA
Via Polvaries, 21
33030 - Buia (UD) - Italy
www.friulfiliere.itThermal break profile
ing a better accession of the varnish.
The glue insertion system assembles the
glue wire into the profile automatically,
unwinding it from 16 small coils. The
extruded thermal break profile presents
mechanical characteristics of resistance
similar to aluminum but ensures high
thermal insulation performance..