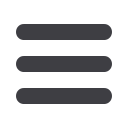
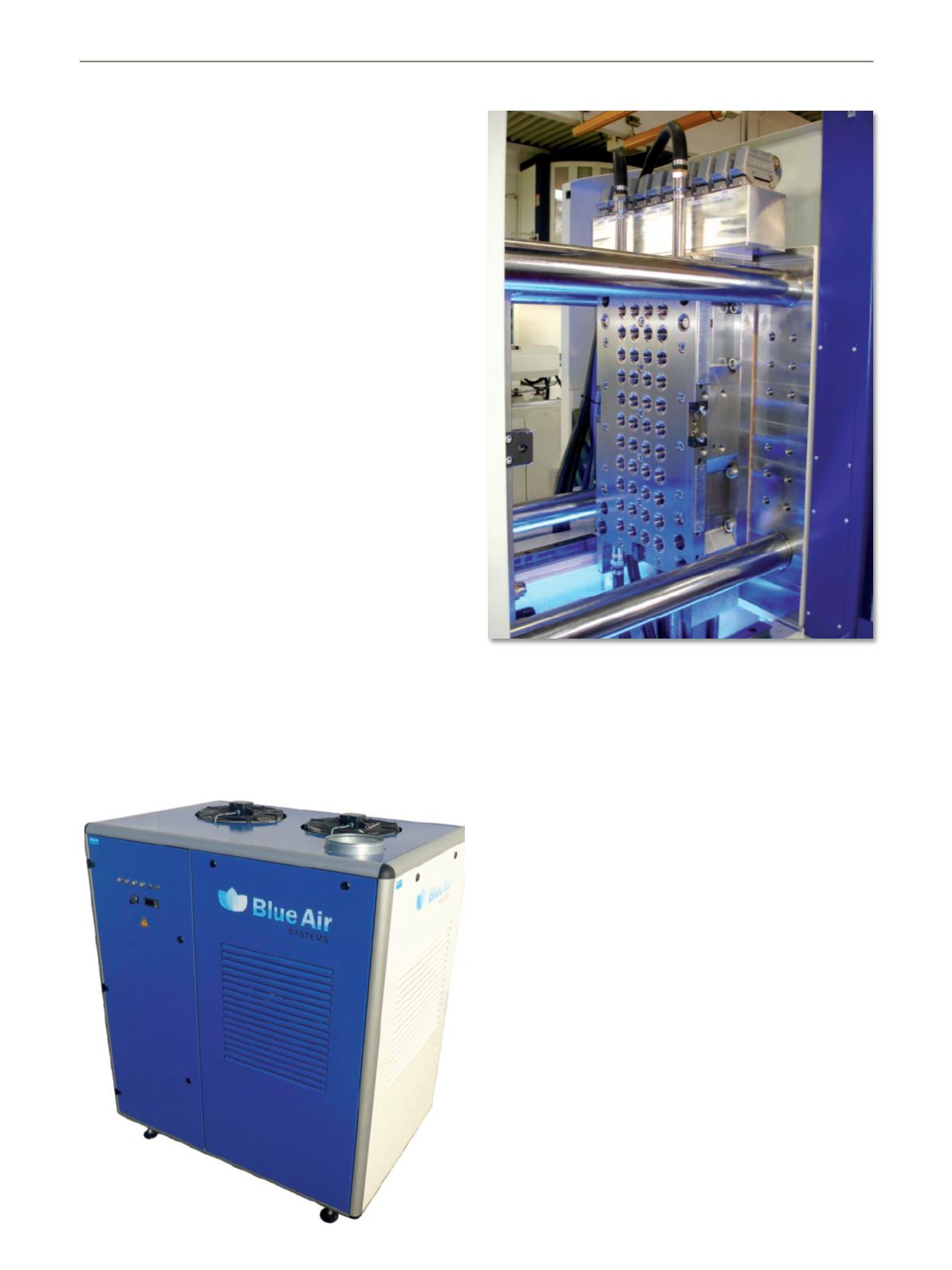
rianten ist, dass nicht eine konstant heiße und feuchte Umge-
bungsluft entfeuchtet wird, sondern dass die Luft in einem
geschlossenen Kreislauf das Werkzeug umströmt. Auf diese
Weise ist kein hoher Energieaufwand zur Entfeuchtung der Luft
notwendig, da die ins DMS zurückströmende Luft bereits zum
Teil trocken ist. Dieser Vorgang erlaubt den Entfall eines Vor-
kühlers (Chiller) und somit wird kein Kühlwasser für das DMS-
Entfeuchtungssystem benötigt. Durch einen Kältemittelverdich-
ter der neuesten Technik wird die benötigte Energie für das
Kühlsystem automatisch reduziert, sobald die Luft trockener
wird. Es wird somit nur elektrische Leistung für das Kühlsystem
benötigt.
Modellrechnung: Werkzeugentfeuchtung mit nur
15 % Energieeinsatz gegenüber einer konventionellen
Strategie
Marktgängig wird eine Entfeuchtungsanlage mit Vorkühlung
(Chiller) angeboten. Beim Einsatz einer DMS-Entfeuchtungsan-
lage kann auf die Vorkühlung verzichtet werden, was eine oft
15.000 bis 20.000 EUR-Investition einspart. Dieser Vorkühler
verbraucht, bei den Standard-Entfeuchtungsanlagen, circa
66 % der benötigten Energie (Energieaufwand im Chiller).
Durch den Wegfall dieses Vorkühlers ergibt sich eine immense
Kosten- und Energieeinsparung. Im laufenden Betrieb werden
dann die Einsparungen augenfällig: Rechnet man beispielsweise
eine gewünschte Kühlkapazität für eine Entfeuchtungsanlage
mit 38.700 kcal/h (45 kW), so ergeben sich 45 / 3 = 15 kW als
notwendige elektrische Leistung für den Chiller. Für die Regene-
rationsheizung, Antrieb und Gebläse werden noch circa 20
kW/h elektrische Energie kalkuliert. Der gesamte Stromver-
brauch für den Betrieb der Entfeuchtungsanlage (Strom für Chil-
ler inkludiert) beläuft sich pro Stunde dann auf 15 kW/h + 20
kW/h = 35 kW/h. Dem steht ein erheblich reduzierter Verbrauch
einer DMS-Entfeuchtungsanlage gegenüber: Die DMS-Anlage
benötigt im Vergleich nur 5 kW. Der Unterschied liegt folglich
bei 30 kW/h oder um es klarer auszudrücken: Eine DMS-Anlage
verbraucht um circa 83 % weniger Energie (5 kW gegenüber
35 kW). Ein gewaltiger Unterschied also. Kalkuliert man die
Energiekosten mit zum Beispiel 0,15 EUR/h, so ergibt sich in ei-
ner Woche bei einer „24/7-Produktion“ mit 168 Stunden Pro-
duktionszeit eine Ersparnis wie folgt: 30 kW x 0,15 x 168 h =
756 EUR pro Woche, also 3.024,00 EUR pro Monat. Man spart
Kosten, Tag für Tag. Bei diesen Einsparpotenzialen wird schnell
klar, dass sich eine DMS-Anlage sehr schnell amortisiert.
Energie sparen und effektiv entfeuchten mit der DMS-Serie
Die DMS-Serie überzeugt durch eine wesentlich vereinfachte
Installation, andererseits aber auch durch einen signifikant
niedrigeren Energieverbrauchs mittels des Einsatzes von Kälte-
kompressoren und Lüftern der neuesten Generation, die sich
durch intelligente Sensorik den klimatischen Umgebungskondi-
tionen kontinuierlich anpassen. Somit entfallen isolierte Was-
serleitungen vom oft weit entfernten Kaltwasserspeicher zum
Entfeuchtungsgerät und zurück. Es genügt die Anbindung an
das vorhandene Stromnetz. Wenn die bestehende Kaltwasser-
kapazität nicht ausreicht, entfällt zusätzlich noch die Notwen-
digkeit, ein neues System zu installieren. Der Verarbeiter spart
Hochleistungswerkzeuge können mit der DMS-Serie effizien-
tere und effektivere Zyklen erreichen (Bildquelle: HTW
Formen- und Fertigungstechnik GmbH – Ludesch, Österreich)
Die kompakte DMS-Serie (Dry Mould System) kann aufgrund
des geringen Footprints leicht und ohne großen Installati-
onsaufwand in die Fertigungszelle integriert werden
32
Peripherie, Werkzeugentfeuchtung
Extrusion 2/2016