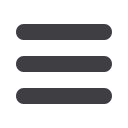
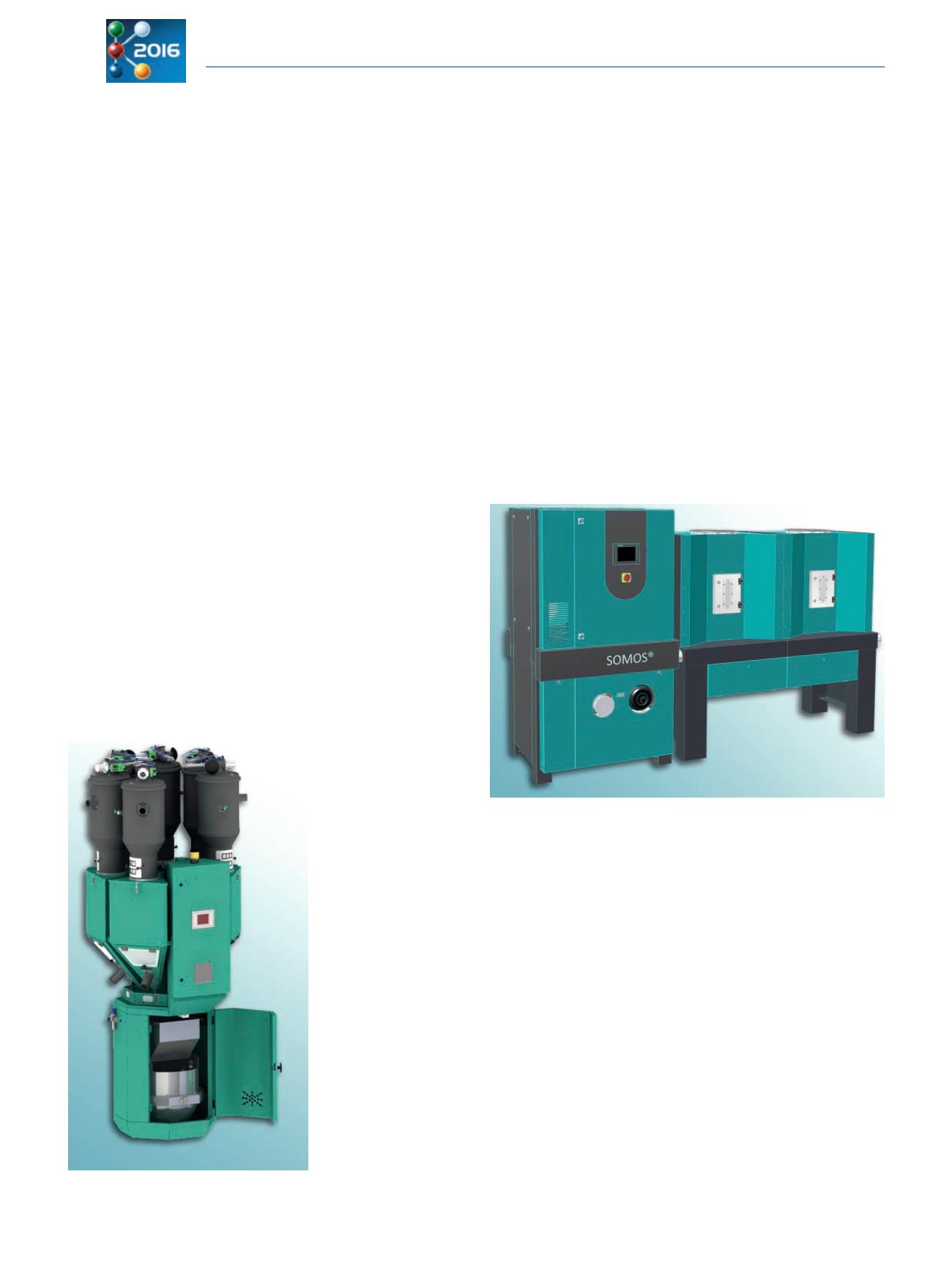
ProTec Polymer Processing:
efficient materials
handling of LFT compounds
W
ith the high-performance, energy-efficient plant and sy-
stems for pre-processing flowable plastics presented at
K 2016, ProTec Polymer Processing now covers the entire pro-
cess chain from conveying and drying to metering and mixing
whether
for injection moulding or for extrusion. A second focus of Pro-
Tec's presence is its abilities as a one-stop shop supplier of
long-fibre-reinforced thermoplastics (LFT) lines covering the
full gamut from planning via construction to commissioning.
New developments presented for the first time at K 2016 in-
clude the SOMOS
®
Batchmix XL batch metering unit for
throughputs of up to 1,920 kg/h and the stationary SOMOS
®
RDT-200 dry air dryer for moderate throughputs.
The SOMOS
®
Batchmix XL metering and mixing system is suit-
able for feeding multicomponent mixtures to both injection
moulding machines and extruders and is designed to handle
up to six flowable components. It can be equipped with
SOMOS
®
suction conveyors for automatically filling material
storage hoppers. A SOMOS
®
control/professional touchscreen
controller with a graphical user interface ensures user-friendly
operation and is also capable of simultaneously controlling ex-
truder throughput. The Batchmix M for throughputs of up to
240 kg/h and the Batchmix L for throughputs of up to 1,100
kg/h of a homogeneous multicomponent mixture complete
this range of gravimetric batch dispensing systems. The new
SOMOS
®
Batchmix unit offers high metering accuracy at an
attractive price/performance ratio.
The new SOMOS
®
RDT-200 stationary dry air dryer has an ef-
fective dry air throughput of 140 to 300 m³/h, enabling highly
economical processing of material volumes in excess of the
throughput capacity of the SOMOS
®
RDM mobile auxiliary dry-
ers (dry air throughput of at most 140 m³/h). The dry air ge-
nerator and the drying vessel are also of a new design. The
drying vessels, which are square on the outside and cylindrical
on the inside, can be fitted together to form a compact mo-
dular drying system comprising up to at most six vessels in gra-
duated sizes with effective hopper volumes ranging from 50 l
to 300 l. Another new feature is the SOMOS
®
control excel-
lence dryer controller with its user-friendly touchscreen ope-
ration which offers numerous drying parameters tailored to
the specific material as well as versatile documentation functi-
ons. To minimise energy consumption, the dryer is equipped
with the tried and trusted energy-saving technology known
from SOMOS
®
dryers: automatic adaptation of drying air vo-
lume to material throughput (ALAV) and the SUPER SOMOS
control mechanism which adapts desiccant regeneration to
the particular moisture loading of the adsorbent. Drying tem-
peratures of 40 °C to 180 °C at a drying air dew point tem-
perature of approx. -35 °C are standard.
The new SOMOS
®
Batchmix XL gravimetric batch metering unit is
designed for a maximum of six components and throughputs of up
to 1,920 kg/h
The new SOMOS
®
RDT-200 stationary dry air dryer with its new
design can provide a variable dry air throughput of
140 to 300 m³/h for economically processing
moderate material throughputs
Extrusion International 5/2016
54