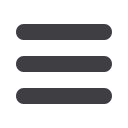
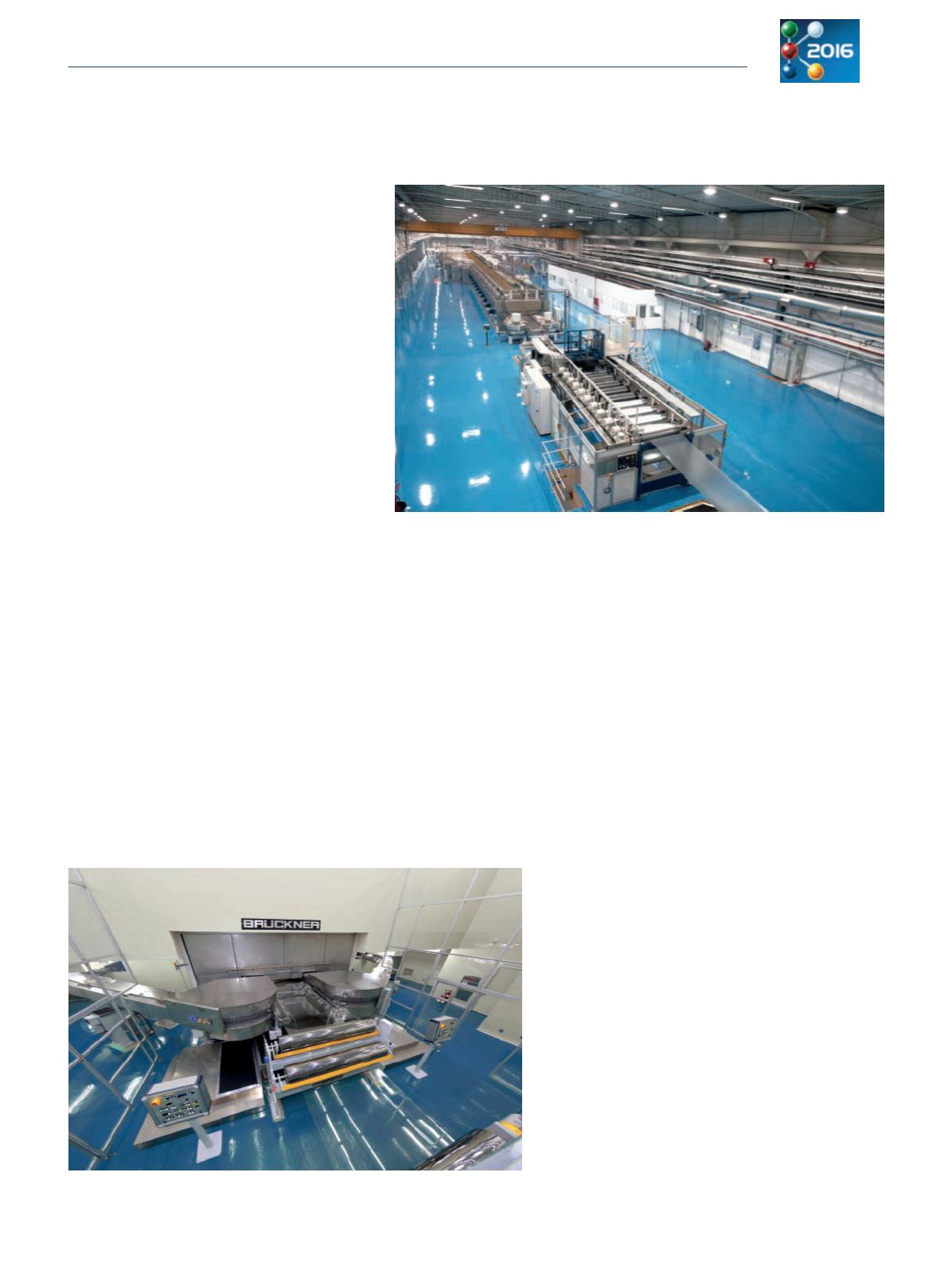
delivery) or “energy monitor”
Film producers will find it easier to produce the highest film
quality all over the world, independent of surroundings, time,
climate and weather conditions.
BOPET lines with 10.4m working widths
Nowadays the established working width for lines that pro-
duce biaxially stretched polyester packaging film (BOPET) is
8.7m. For the K 2016 Brückner Maschinenbau will present a
10.4m concept for the first time ever in the world. This will
fulfil the demands for higher productivity in BOPET produc-
tion: The new lines convince with around 20% more output
capacity with the proven speeds of up to 515m/min. Film pro-
ducers can hereby profit from Brückner Maschinenbau’s ex-
perience from many successful projects with over 10m
working widths, from fewer specific production costs as well
as reduced energy consumption and therefore better
overall profitability.
Lower operating costs with higher efficiency
Brückner’s newly designed sliding system for trans-
versely stretched film means speed increases from over
600m/min. At the same time newly developed mate-
rials led to a reduction of the lubrication use by more
than 50%. The new design in combination with newly
developed lubrication is the basis for lower production
costs. Furthermore these newly developed lubrication
materials are also available for upgrades on current
high-performance lines.
A new winder system caters for higher line efficiency.
In the future Brückner lines can take 40% more win-
der length by increasing the winder diameter from
1.55m to 1.8m. More winder length means fewer roll
Brückner:
improving the efficiency of film lines
Intelligent Line Management
Continually increasing speed and output with
ever shorter delivery times and growing demand
for quality make running a film stretching line a
highly complex business. Film producers and
their operating personnel stand before increa-
sing challenges when it comes to guaranteeing
a stable and efficient production with the hig-
hest quality film.
This is where Brückner’s “Intelligent Line Ma-
nagement” (ILM) comes in. This is an integrated
solution which smooths the way for Brückner’s
customers’ “Smart Production” and “Industry
4.0”. The focus lies here on a new way of ope-
rating lines, putting the emphasis on the process
view as opposed to the usual machine view. This
new operating concept is supported by an in-
creasing amount of assistant systems.
Along with the “Energy Monitor” which is al-
ready used to monitor energy consumption at all line compo-
nents, Brückner has developed new tools and assistant systems
for inline measurements and to directly influence important
film values such as temperature, haze, molecular orienteering
angle or also density and porosity. For film production this
brings a variety of advantages:
• Simplified line operation with significantly fewer process pa-
rameters to adjust and intuitive user guidance
• Transparency and traceability of production data
• Targeted inline control of film properties for a consistently
high film quality
• Increased line availability through shorter reaction time in
case of malfunctions
• Efficiency, productivity and flexibility through assistant sy-
stems such as “fast product change” (key word: Just-in-time-
Extrusion International 5/2016
51