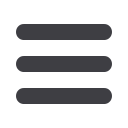
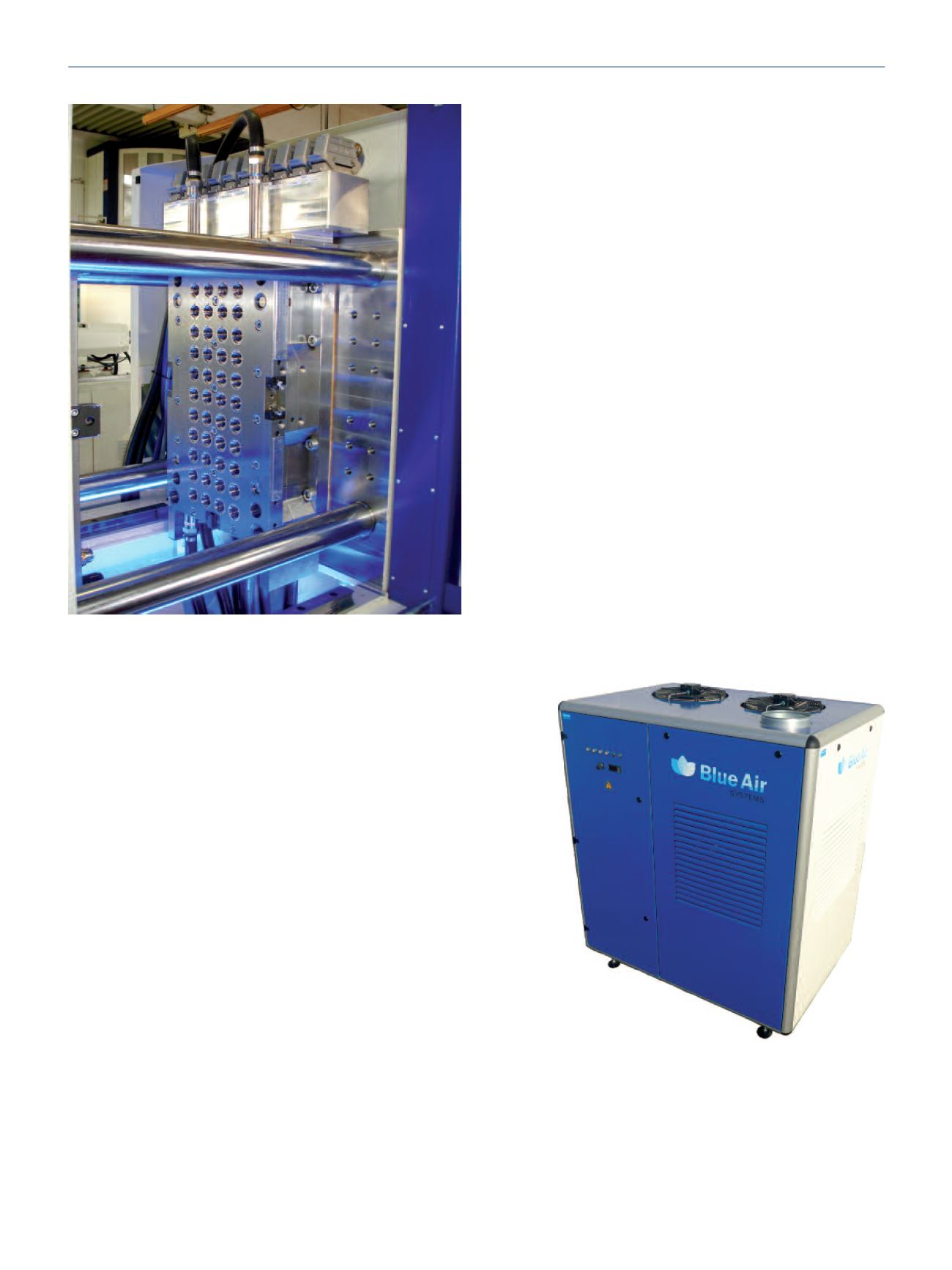
ond time during operation. The DMS is a tailor-made system,
allowing the manufacturer to choose to supply dry process air
volumes from units ranging 500 to 3.500 Nm³/h.
Smart dehumidification with the DMS Series
The DMS units are made of high quality, perfectly balanced
components to allow optimal energetic mould dehumidifica-
tion. Until now, no comparable systems exist on the market.
The process air is run in a closed loop, always brought back to
the DMS unit for pretreatment and dehumidification of the air
down to a 3°C dew point. The process air is dried by simulat-
ing a cold object in the DMS unit (similar to the mould) that al-
lows the moisture in the air to condensate in the DMS unit,
before it reaches the mould. The DMS unit cools and dehu-
midifies the air in a 2 step refrigerant unit with the MPCSC
technology (Micro Processor Controlled Segment Condensa-
tion). For this version, only electrical energy is needed. A DMS
15 supplies a nominal process airflow of 1.500 Nm³/h. The
larger DMS 25 dehumidifies 2.500 Nm³/h and the DMS 25+
up to 3.500 Nm³/h. Just like the ecological footprint, the ac-
tual footprint left in the production hall with the dimensions
of a DMS 15 of 900 x 1300 mm is remarkably small.
Sophisticated areas of application
The DMS units are designed for all applications where sophis-
ticated, high-performance moulds are cooled with chilled
water and which are located in areas where moisture in the air
can condensate on the mould. So, generally speaking, all in-
jection molding, extrusion blow moulding and thermo form-
ing systems. Core areas in the plastics industry are packaging
systems such as caps and PET performs, as short cycle times of
the process and high production outputs require chilled water.
Bernhard Stipsits, managing director of Blue Air Systems: “The
DMS units from Blue Air Systems guarantee condensation-free
production conditions in a closed system, even when using
very low chilled water temperatures for the moulds through-
out the year, being independent from ambient climatic
weather conditions. The MPSCS (Micro Processor Controlled
Segment Condensation) technology provides controlled pa-
rameters at all times, making sure the optimal energetic con-
ditions are automatically adjusted. What you get is higher
productivity and consistent product quality in the production
process at the lowest possible energy consumption. It’s time to
start reducing our ecological foot print and the DMS is a huge
step in this direction!”
High quality moulds can achieve maximum performance as well
as efficient production cycles with the DMS units
(Source: HTW Formen- und Fertigungstechnik GmbH – Ludesch,
Austria)
The compact DMS series can easily be integrated into a
manufacturing cell due to the marginal foot print it leaves
behind, physically as well as ecologically
www.blue-air.atExtrusion International 3/2016
39