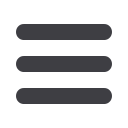
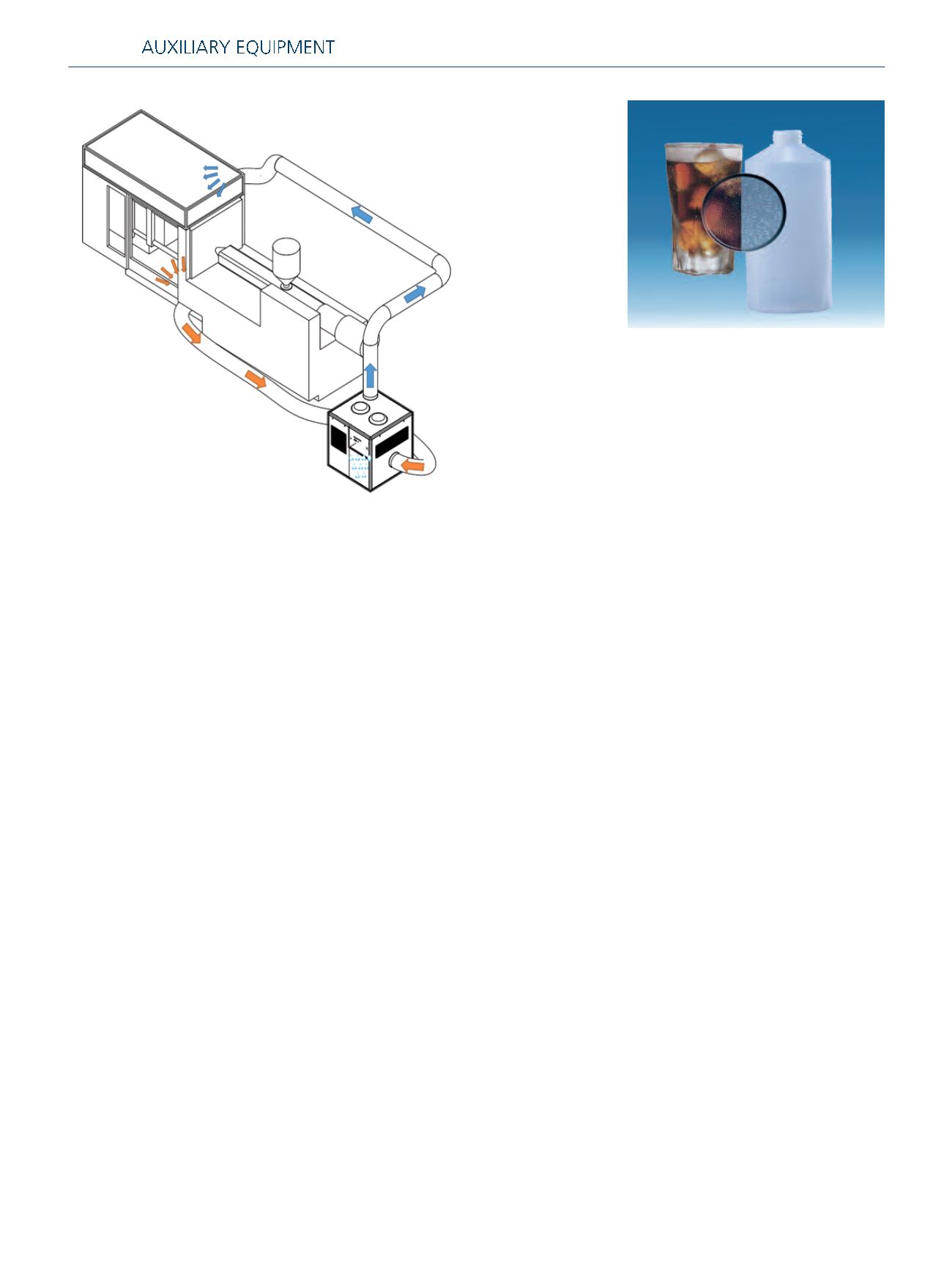
dehumidifier, the manufacturer also needs to take the cost of
a new chiller, or the extension of the existing chiller system,
into his investment calculation.
A look at the new, waterless DMS (Dry Mould System)
in a closed loop
The DMS unit dries air on the basis of the condensation prin-
ciple. The main difference to the standard systems is that the
DMS is not constantly dehumidifying hot and humid ambient
air. Instead, dry process air is circulated around the mould in a
closed loop, bringing the air back to the DMS unit. By doing
this, there is no necessity of using high cooling loads to dehu-
midify air, as the air returning to the DMS unit is partially dried.
This procedure allows the DMS to work without a pre-cooler
(chiller) and therefore no chilled water is needed for the DMS
dehumidification.
A state-of-the-art refrigerant compressor of the newest tech-
nology automatically reduces the needed cooling capacity, as
soon as reduction of moisture in the air is detected. Therefore,
the DMS only uses electricity for the actual cooling need of
the refrigerant system.
Model calculation: mould dehumidification with only 85 %
lower energy consumption, compared to conventional systems
Standard dehumidification systems on the market are supplied
with a water pre-cooler. The DMS units do not need the chilled
water for pre-cooling, which automatically reduces overall in-
vestment costs for such a system between 15.000 and 20.000
Euros. A pre-cooler in standard systems, requires only 66 %
or less of the overall energy normally needed.
By cutting out the pre-cooler, immense cost and energy sav-
ings can be achieved. In production, the actual savings can
seen: For example, a dehumidification unit with a desiccant
wheel and a process air volume of 1.800 Nm³/h needs a cool-
ing capacity of 38.700 kcal/h (45 kW) (calculated at ambient
conditions of 35°C/ 60% rel. hum.), which adds up to 45 / 3
= 15 kW of electrical energy needed to run the chiller. For the
regeneration heater, blower and motors, an additional 20 kW
of electrical energy is needed for the dehumidifier. The total
electrical consumption of the dehumidification and the elec-
tricity for the chiller adds up to 15 kW/h + 20 kW/h = 35 kW/h.
This is a large amount of energy when compared to the DMS
unit, which runs with an average of 5 kW, as only electrical
energy is needed for the refrigerant compressor and the ven-
tilators. The difference of 30 kW/h or in other words, 86 %
reduction, is extreme.
If you calculate for example 0,15 EUR/kW and consider a 24/7
production with 168 hours production time per week, the im-
mensity of the savings becomes clear: 30 kW x 0,15 x 168 h
= 756 EUR per week, or 3.024,00 EUR per month (á 4 weeks).
Hard earned money is saved so easily, day by day, every day. It
is just as easy to calculate the short amortization time of the
DMS unit.
Effective mould drying with the DMS means
you save large amounts of energy, too
The installation of the DMS unit is easy and effective. The in-
stallation of insulated water pipes to and from the chilled
water source is no longer necessary. Only the connection to
the electricity supply is required. With the application of re-
frigerant compressors and ventilators of the youngest gener-
ation, significant energy savings can be achieved. These
systems control and adapt the required cooling capacity to the
ambient conditions, with the help of intelligent sensor tech-
nology. If the chilled water capacity is not enough, with the
DMS application, no extra investment into an additional chilled
water supply is necessary. The manufacturer has the advan-
tage of saving double, once with the investment and a sec-
Condensation-free production conditions with the DMS unit:
dry air circulates around the mould in an enclosed
environment – more performance, less energy and
consistent product quality
Uniform product
quality with
condensation-free
production
conditions
Extrusion International 3/2016
38