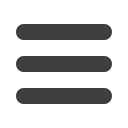
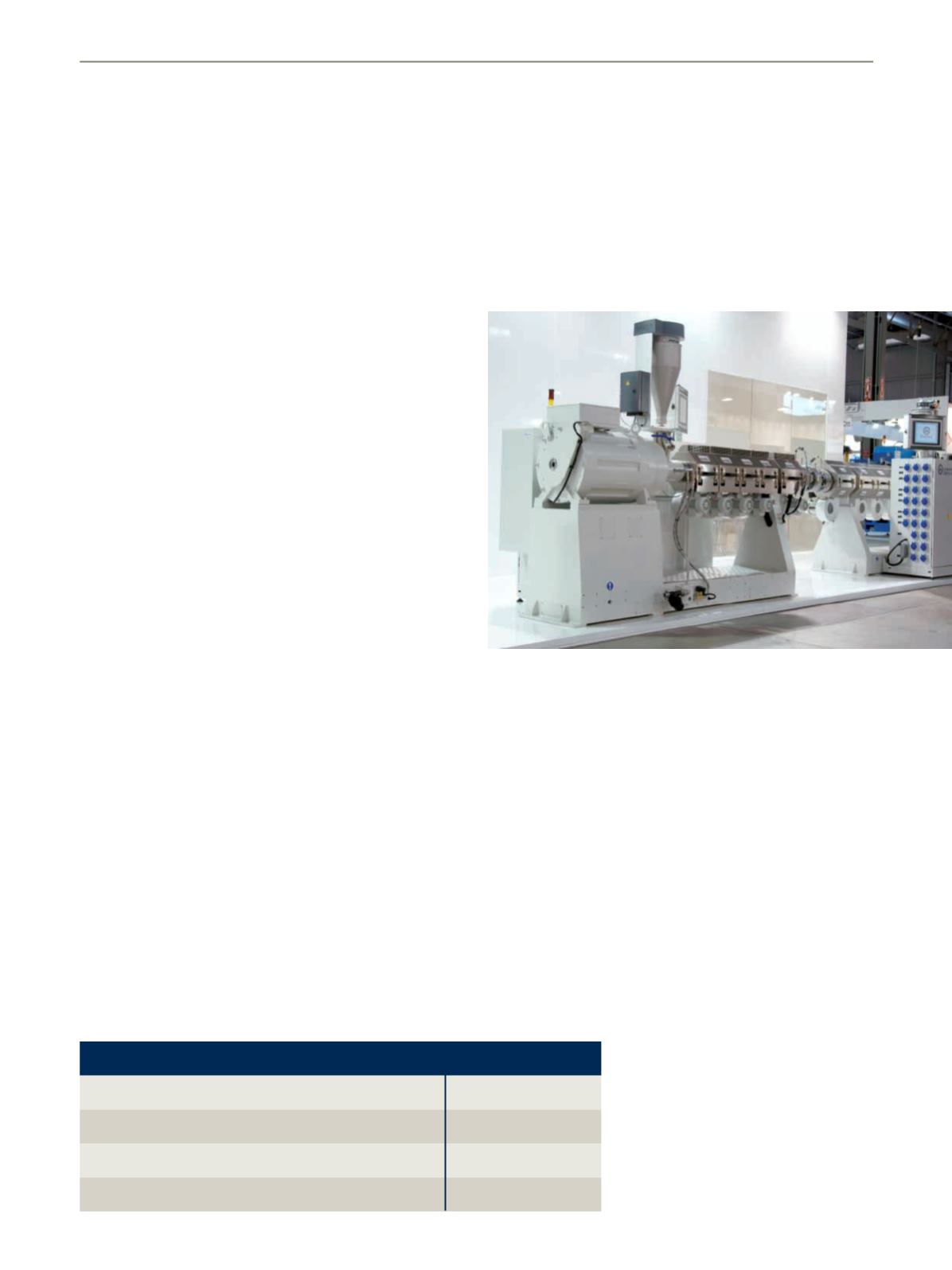
Pipe manufacturers have started to think
in terms of operation cost efficiency, but
without compromising the performance of
the pipe extrusion lines. Tecnomatic, which
will celebrate its 45 years of experience in
the plastic sector, will present at the
K 2016 show innovative solutions in pipe
extrusion, to assist customers not only by
supplying extruders and die-heads but as
well providing complete production
systems for a business which is getting
increasingly demanding.
A
t K-show 16’ Tecnomatic will introduce a further develo-
ped version of its extrusion series ZEPHYR in L/D 40, both
in a gearless and a traditional version (with gearbox).
ZEPHYR is the most performing extruder of Tecnomatic’s pro-
duct range, it boasts an array of advanced technical solutions
which makes them unique models designed for pipe producers
looking for even more focused energy saving machines, offe-
ring extreme output performance at lower melt temperatures.
The innovation spans the entire extruder and includes new spi-
ral grooved bush, screw and motors.
Pipe extrusion is highly dependent on electricity and most of
the energy usage is in operating the extruder. The Zephyr series
has made this the utmost priority offering extruders with in-
creased screw length and smaller torque and AC water cooled
motors, to assure same output of bigger size extruders but with
a better energy efficiency.
Advanced Solutions for Pipe
Manufacturers aiming at Energy
and Performance Efficiency
44
Pipe Extrusion
Extrusion 7/2016
ZEPHYR 45.40 – 500 Kg/h
The new feed bush ensures minor friction, commonly genera-
ted by raw material transport, with subsequent increasing of
the specific and total throughput. The further development in
screw design, with optimization and enhancement of torque
and shearing elements, have improved the output but have al-
so led to process the material at lower melt temperatures.
To meet the requirements for production efficiency the machi-
nes are equipped with torque or water-cooled motors (in this
case with one or two steps gearboxes) and compact water-coo-
led inverters. These solutions combined with the mechanical
features ensure outstanding power consumption levels, low
noise operation (< 74 Db), reduction of workload for mainten-
ance, higher efficiency within wide speed and load ranges, and
faster dynamic response.
A comparison between a gearless extruder in size 60.37 and
new Zephyr 60.40 is clearly showing the advantages in the ad-
option of this last solution. (
Table
)
Extruder Comparison in % (ZEPHIR 60.40 vs. ZEUS 60.37
Max. screw speed (RPM)
0%
Max. Output*
+42 %
Installed power (Kw)
+24 %
Energy consumption** at 550 kg/h (Kw/h)
-13 %
* Zeus 60.37 at 500 kg/h, Zephyr 60.40
at 800 kg/h
** Below 140 KW/h/Kg for extruder
Zephyr 60.40 at 500 kg/h