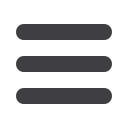
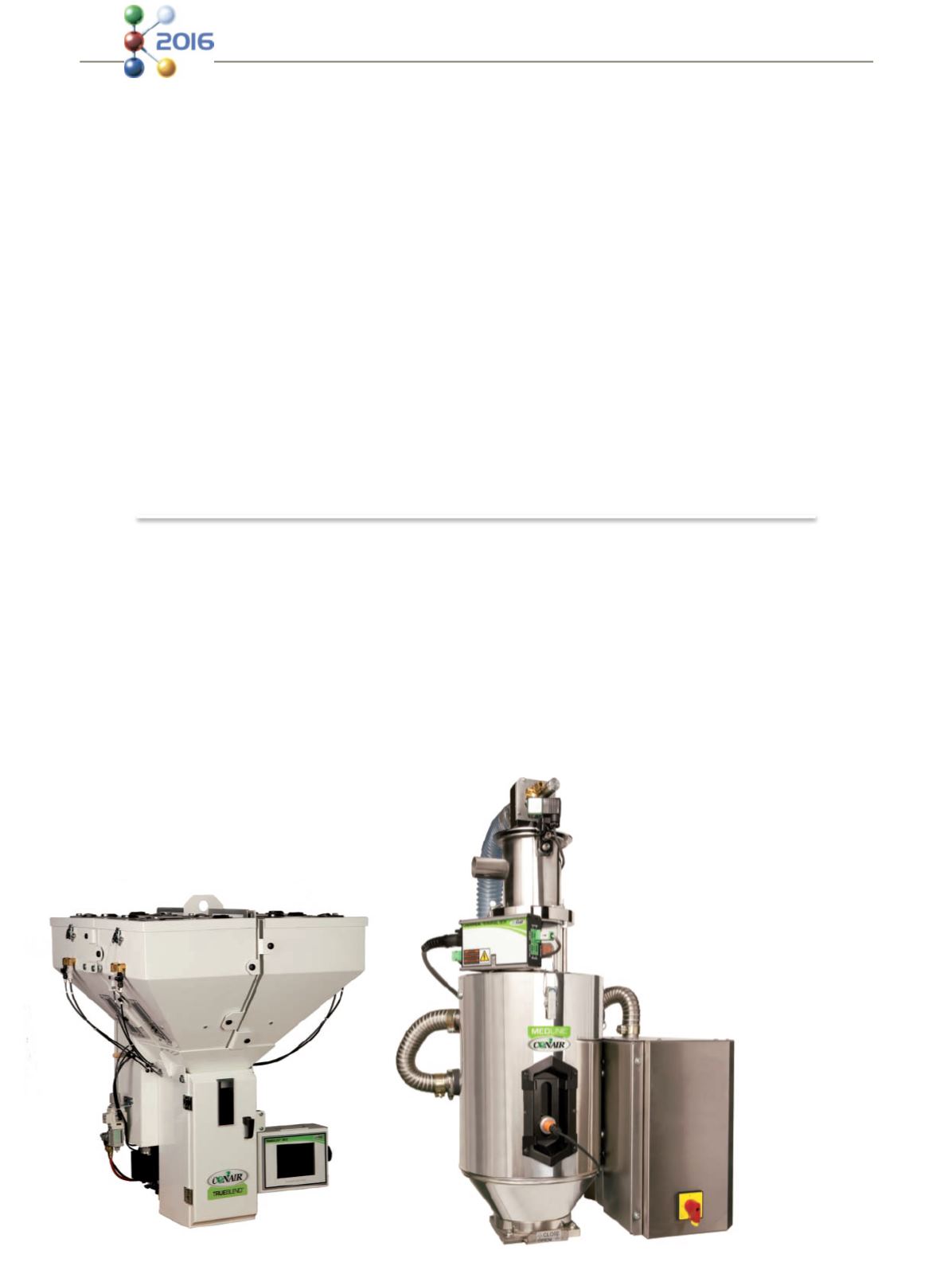
➠
Rolf Schlicht GmbH
www.schlicht-gmbh.deK 2016: Halle 3, Stand A35
hohe Präzision bei schneller Amortisation der Investition. Ver-
bindet man das MCWeight mit einem oder mehreren gravime-
trischen Dosiergeräten Typ MCBalance, so erhält man ein
äußerst präzises selbstregulierendes Additivdosiersystem für
Extruder: Das MCWeight registriert selbst kleinste Leistungs-
schwankungen des Extruders und passt die Leistung der Dosier-
geräte entsprechend an. Weitere Informationen:
https://www.movacolor.comK 2016: Halle 11, Stand D58 oder am Rolf Schlicht-Messestand
n
Reinigungsgranulat
: Neben den bewährten chemischen
Reinigungsgranulaten RAPID PURGE PM9240 und PM5540
sind die mechanischen Reinigungsgranulate MP1000 und
MP900 lieferbar, die für leichtere Reinigungen auf Spritzguss-
maschinen, Extrudern und Blasformanlagen entwickelt wur-
den. Diese RAPID PURGE Typen sind gebrauchsfertige Reini-
gungsgranulate, müssen daher nicht mehr gemischt werden
und decken alle Thermoplastgruppen ab. Des Weiteren bietet
man drei neue FDA/GRAS konforme Reinigungsgranulate an:
Die Typen Rapid Purge RE9240, RE5540 und RE8240 wurden
speziell für den Lebensmittel- und Medizinbereich entwickelt.
Auch diese RAPID PURGE Typen sind gebrauchsfertige Reini-
gungsgranulate und müssen daher nicht gemischt werden.
Das RAPID PURGE IG 3000 ist ein chemisch wirksames Konzen-
trat für Spezialanwendungen, das eine genaue Abstimmung
auf die verarbeiteten Kunststoffe ermöglicht. Vor Gebrauch
werden das IG 3000 mit dem verarbeiteten Kunststoff ge-
mischt.
Das RAPID PURGE R5000 in Pulverform wird mit einem Kunst-
stoffgranulat gemischt. Hervorragend geeignet ist hierzu Mahl-
gut des verarbeiteten Kunststoffs.
Sämtliche Reinigungsgranulate von RAPID PURGE sind abrasi-
onsfrei und enthalten keine Glasfasern.
Die Reinigungsgranulate decken einen Temperaturbereich von
170 bis 410 °C ab. Sie sind nicht giftig und sehr sparsam.
ing System) is a revolutionary new approach to vacuum convey-
ing. Pellets move at slow speeds in dense slugs of material. Ma-
terial speeds can range from as slow as 70 m/min (230 ft/min)
up to 366 m/min (1200 ft/min). This can be compared to con-
ventional high-speed dilute-phase conveying, where 4500
ft/min (1372 m/min) is a typical low speed and speeds up to
829 m/min (6000 ft/minute) are not uncommon. At these high-
speeds, pellets smear against the sides of aluminum tubing, de-
forming and creating long streamers or “angel hair” that can
clog the system. Brittle materials (like styrene or polycarbonate)
can break up and create dust and fines, and
hard pellets, especially abrasive materials like
glass-filled resins, can quickly wear away the
inside of the conveying lines eventually caus-
ing leaks and failure.
The R-PRO system dramatically reduces the se-
verity of all those problems. Comprised mainly
of standard vacuum-conveying components,
R-PRO results in slower flow and less resin
n
The patent-pending R-PRO™ dense-phase vacuum-convey-
ing system developed by Conair to minimize pellet fracturing,
"angel hair" and equipment wear caused by conventional
dilute-phase conveying, will make its first appearance at a
European tradeshow when K 2016 begins in October. Other in-
novations on display will include a new FLX-128 Plus conveying
control, which now can be set up to operate the R-PRO sys-
tem, a new Mobile Drying/Conveying (MDC) system with
standard color touchscreen control interface, and several ex-
amples of equipment from Conair’s new MedLine
®
range of
clean-room-ready auxiliaries.
The R-PRO system (which stands for Resin Protection Convey-
European Debut:
Revolutionary R-PRO™ Conveying System
Examples of
equipment being
offered as part of
the expanded
MedLine
®
family
of products
include a TB45
TrueBlend
gravimetric
blender in medi-
cal white (left)
and MicroWheel
dryer and Tube-
Loader (right)
82
Preview
Extrusion 6/2016