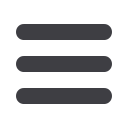
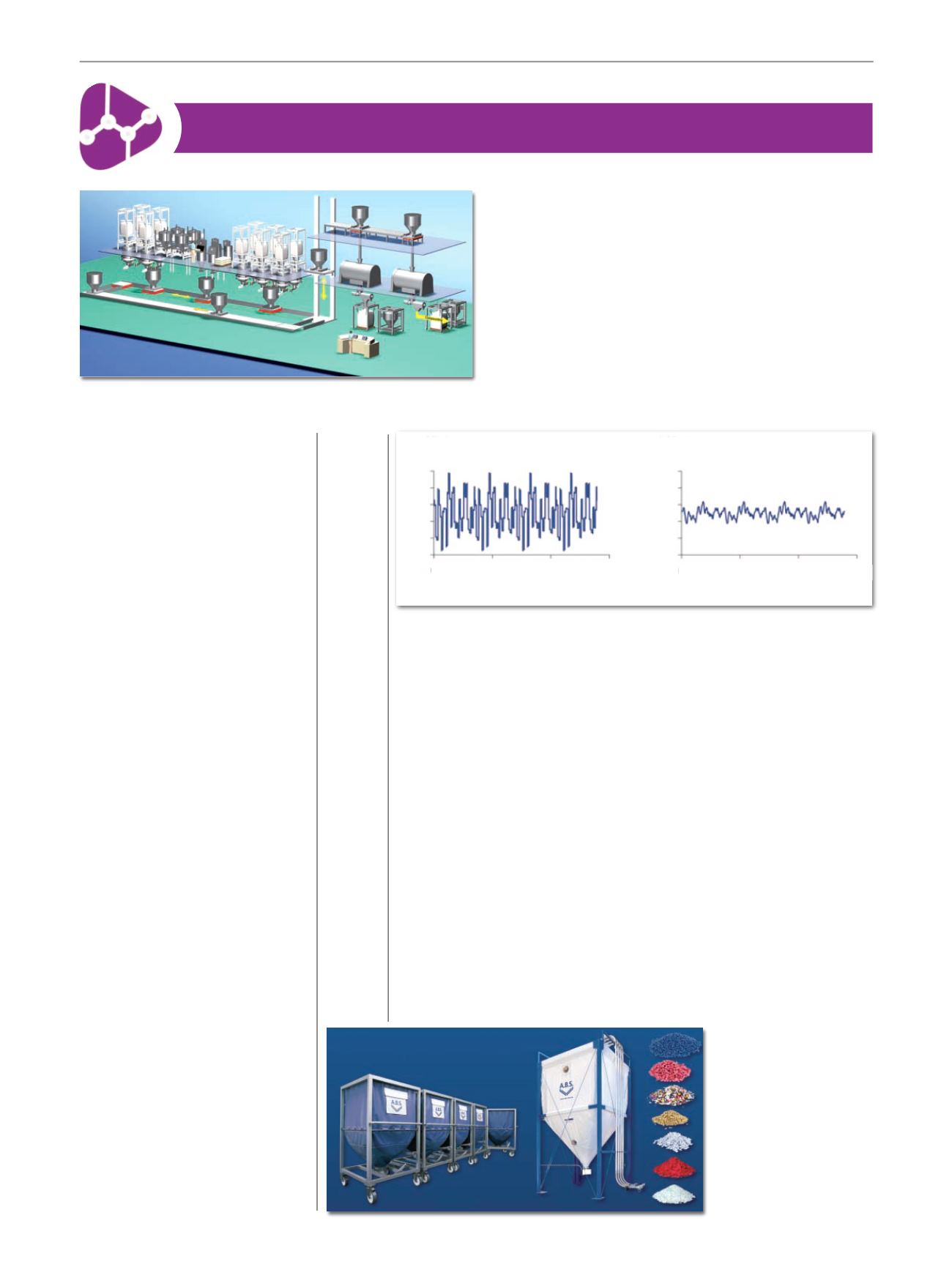
che sich auf die Handlingkosten aus-
wirken, sowie die Aspekte Sauber-
keit und Hygiene. Auch Sicherheits-
aspekte wie Staubemissionen oder
die Zündfähigkeit von Pulvern sind
nicht außer Acht zu lassen. Einfluss
auf die Lagerung sowie später auf
das Fördern haben schließlich die
Materialeigenschaften. Bei hygrosko-
pischen Kunststoffen ist in erster Li-
nie an die Feuchteaufnahme zu den-
ken, was besonders im Sommer pro-
blematisch werden kann. Falls das
Material in Behältern gelagert wird,
kann das
Beschleiern mit Trocken-
luft
eine geeignete Präventivmaß-
nahme sein. Zu den Materialeigen-
schaften zählt schließlich auch das
Fließverhalten, das wiederum von
der Materialart abhängt, beispiels-
weise ob es sich um Granulat, Flakes,
Pulver, Mahlgut oder Fa-
sern handelt. Zu berück-
sichtigen ist ferner, ob
ein Schüttgut frei oder
schlecht fließt, ob es
klebrig, klumpig bezie-
hungsweise
agglome-
rierend
ist oder sich
brückenbildend verhält.
Höchsten Qualitätsanforderungen zu genügen, gleichzei-
tig aber konsequent Kosten zu reduzieren – diesem er-
höhten Druck ist die kunststoffverarbeitende Industrie
permanent ausgesetzt. Deshalb kommt dem Rohstoffma-
nagement beim Lagern, Fördern, Trocknen sowie Dosie-
ren/Mischen höchste Bedeutung zu, angefangen von der
Rohstoffherstellung über die Compoundierung bis hin
zur Verarbeitung. Genauigkeit und Konstanz bei diesen
Etappen vom Silo bis zur Verarbeitungsmaschine sind
Schlüsselfaktoren für Produktqualität und Rentabilität.
Kriterium: Lagern
E
in wirtschaftlich tragbares und
technisch sinnvolles Materialver-
sorgungskonzepts beginnt bei der
Lagerung der Ausgangsstoffe. Zu-
nächst muss es sich an den zu ver-
sorgenden Produktionsanlagen – Mi-
schen, Extrudieren, Compoundieren,
Spritzgießen, Blasformen – und da-
mit an Zahl und Menge der zu be-
vorratenden Materialsorten orientie-
ren. Sie entscheiden, ob Kleingebin-
de (Sackware mit 25 kg/Gebinde)
oder Großgebinde (
BigBags
,
Okta-
bins
mit bis zu 1000 kg) zu lagern
sind, oder sind Silos aus Aluminium
oder Edelstahl doch wirtschaftlicher.
Je nach dem für welchen Einsatz-
zweck die Silos gebaut werden, un-
terscheidet man in
Ein- oder Mehr-
kammersilos, Verladesilos, Misch-
silos
und
Homogenisiersilos
.
Eine besondere Spezies sind Mischsi-
los. Mit ihnen kann man Produktions-
schwankungen bei den Eigenschaften
chargenweise angelieferter Schüttgü-
ter egalisieren, so dass man mit mög-
lichst gleichbleibender Produktquali-
tät produziert. Je nach Anforderung
(kontinuierlich oder diskontinuierlich,
Reinigungsaufwand, geforderte Ho-
mogenität in Abhängigkeit der Misch-
zeit, etc.) und Produkteigenschaft (frei
fließende oder schlecht fließende Pro-
dukte, Granulat oder Pulver, PET-
Flakes, etc.) kann man aus mehreren
Mischkonzepten wählen.
Für Innen werden darüber hinaus
noch
flexible Silos
angeboten. Die
atmungsaktiven Polyestergewebe
Verlauf der
Produk-
tions-
schwan-
kung ohne
und mit
Einsatz
eines
Mischsilos
(Quelle:
Zeppelin)
der Silos weisen eine extreme Reiß-
festigkeit auf, so dass je nach Gewe-
beart bis zu 50 Tonnen in ein Silo ein-
gefüllt werden können. Es wird ein
Vielfaches an Sicherheit bei der Fes-
tigkeitsberechnung berücksichtigt.
Das Silo ist somit für den industriellen
Einsatz bestens geeignet. Geringe
Transportkosten, platzsparende Bau-
weise, Flexibilität bei der Standort-
wahl und genehmigungsfreie Instal-
lation machen diese Silos zu einem
kostengünstigen Lagerplatz für
Schüttgut. Hinzu kommen abhängig
von Bedarf und interner Logistik die
Tagesbehälter
und nicht zuletzt
sind die
Materialaufgabestationen
zu berücksichtigen. Als weitere Ent-
scheidungskriterien gelten der erfor-
derliche Flächenbedarf, Automatisie-
rungsgrad und Transportwege, wel-
Materialhandling
Flex-
Container
und
Flex-Silo
(Werkbild:
A.B.S.)
W
erkbild: AZO
52
BIGfritz: Materialhandling
Extrusion 1/2016
ohne Mischer
mit Mischer
Produktionszeit [h]
Produktionszeit [h]
1
0,8
0,6
0,4
0,2
0
0
50
100
150
0
50
100
150
1
0,8
0,6
0,4
0,2
0
Flex-Container
Flex-Silo