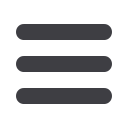
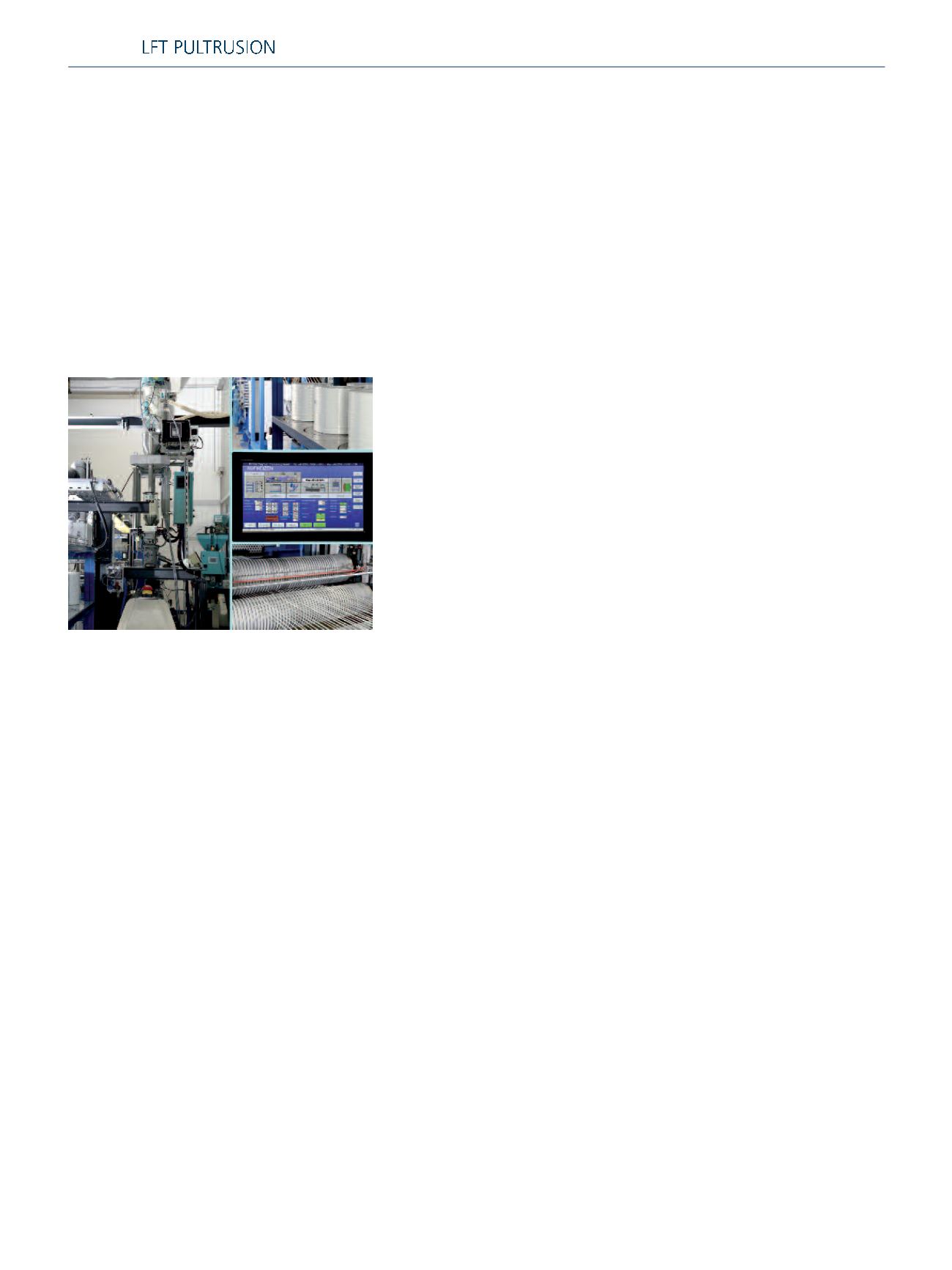
Extrusion International 2/2016
34
www.sp-protec.comVersatile plant engineering for
high quality LFT compounds
W
ith the acquisition of PolymersNet GmbH,
Lampertheim, in late June this year, ProTec Polymer Pro-
cessing also took possession of the pultrusion plant installed
there for producing long-fibre-reinforced thermoplastics (LFT).
The plant has now been rebuilt and extended at ProTec's Ben-
sheim process and materials development technology centre
where it can also be used for carrying out specific customer
tests. A new, central component of the plant is a high-perfor-
mance compounding extruder and the plant controller has also
been designed for automated operation of all process steps.
With these new facilities, the LFT plant has restarted operation
with trials commissioned by clients; further development activi-
ties are already in the pipeline. When injection moulded, LFT
compounds with glass, steel or carbon fibre reinforcement along
the length of the pellets result in high-strength, lightweight com-
ponents which simultaneously have very good surface quality.
Any conventional thermoplastics or even biopolymers such as
PLA (polylactic acid) can be used as the matrix. "With focused
know-how along the entire LFT process chain, ProTec has es-
tablished an efficient structure for this high-performance tech-
nology. We are now a one-stop shop for our current and future
clients, offering everything from materials development to test-
ing and commissioning of a tailor-made LFT pultrusion plant. We
design plants for fibre contents of up to 60 wt.% and through-
puts of up to 1,200 kg/h, and all at a fair market price", explains
Managing Director Peter Theobald.
The new compounding extruder installed in the LFT develop-
ment plant at Bensheim with its co-rotating, 26 mm diameter
twin screws is designed for throughputs of up to 150 kg/h. In-
stalled upstream of the extruder is a SOMOS
®
Gramix S gravi-
metric dosing system for accurately dosing and mixing of up to
nine components. As a result, a very wide range of individual
formulations of the polymer matrix can be produced very flexi-
bly directly in the process. Recycled material and additional fillers
may likewise be included in the material formulation. The LFT
plant's impregnation die, where the fibre strands are spread
apart and enveloped with polymer melt, is designed in such a
way that, even at recycled material contents of up to 10% in
the melt, consistently high quality impregnation of the fibre fil-
aments is achieved. The various different creels required for un-
winding glass and carbon fibres in the pultrusion plant are also
available.
LFT compounds - produced by pultrusion
LFT compounds are produced by pultrusion which involves con-
tinuously drawing fibre strands through a polymer melt, so im-
pregnating the individual fibres with the polymer matrix and,
once the resultant fibre/polymer strands have cooled, pelletising
them. LFT pellets for injection moulding are conventionally
around 10 to 12 mm in length. Pellets 25 mm in length (LFT
compounds with extra-long fibres) are used for compression
mouldings. In the first impregnation process step, the fibre
strands are guided from the creels by a specially designed guide
into the impregnation die.
Downstream from the die, the hot fibre/polymer strands are then
finally shaped, for example into round strands or flat tapes, in a
profiling system. After cooling in a cooling unit appropriate for
the polymer, they pass through a puller before finally being fin-
ished. It is the puller which controls continuous operation of the
plant, the tensile force it applies to the fibre strands extending
right through the impregnation die to the point at which the
strands are unwound from the individual fibre bobbins.
The LFT plant and all its modules are operated from the central
plant controller. Controlled variables include line speed, extruder
throughput, pellet chopping length and, if required for the par-
ticular application, other up- and downstream functions of the
overall plant.
LFT pultrusion
plant at ProTec's
Bensheim
technology
centre –
designed for
developing
high-quality
long-fibre-
reinforced
compounds
with many and
varied polymer
matrices and
reinforcement
fibres (photo:
ProTec Polymer
Processing)