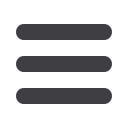
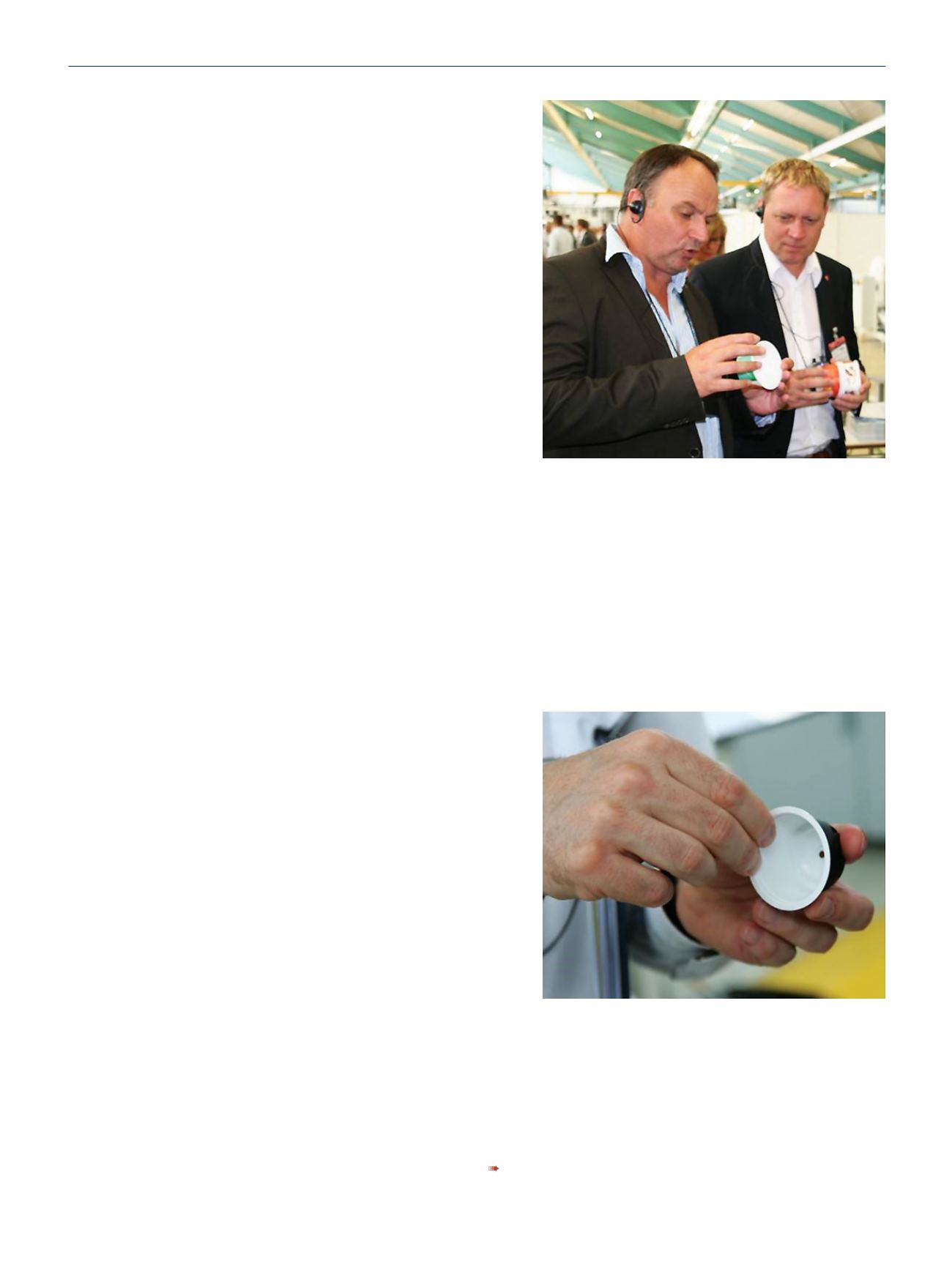
35
Extrusion International 4/2016
Coffee capsules made of multilayered PP
Among the various demonstrations,
the visitors took special interest in
the IML-T decoration
ket demand for in-mold labeling decoration and,
above all, the good economic development in non-
European markets. In the coming years, Schäuble
sees the demand for more automation and hy-
gienic production processes as the main driving
forces of development in the industry: “We expect
the increase in the cycles per minute of ILLIG ma-
chine lines will continue to be a decisive factor in
the near future for high lot-size productions and
highly automated production processes. To accom-
modate this market demand we will continue to
improve the cpm-speed in the thermoforming and
trimming process, as this will further improve the
quality and reliability of the formed parts.” To this
end, the installation of camera-assisted quality as-
surance systems will be a contributing factor. Re-
peated cleaning intervals necessitated by increased
hygiene standards are a constraint on productivity,
for which ILLIG is also developing solutions.
Of particular interest among the live machine dem-
onstrations was the IML-T on the RDM 70K produc-
tion line in combination with the specially designed
RDML 70b unit: Every hour 17,280 rectangular
cups made of polypropylene were produced on an
18-cavity mold that included picture-perfect deco-
rated labeling on all four sides and the bottom of
the cups during the forming process.
New at this year’s Open House was the latest-gen-
eration RV 74d automatic vacuum forming machine
with enhanced performance in direct comparison
with the previous version. The forming area has
been extended, the forming pressure increased
by 50% from 2 to 3 bar, and the maximum cycles
per minute increased to 40 cpm. The part quality
has been further improved by controlled overlap-
ping machine sequences and optimized heating
settings. For demonstration purposes, polystyrene
food trays were formed on the RV 74d using a
6-cavity mold. Some of the special features of this
vacuum-forming machine are its exceptional flex-
ibility, compatibility with cost-effective molds that
can be self-made using the included mold-making
manual, and its high availability.
The same can also be said for the automatic pres-
sure-forming machines RDK, RDKP and RDM-K.
The RDM-K-series cup machines deliver unrivaled
solutions for the reliable reproduction of the ther-
moforming process and its control, currently not of-
fered by any other thermoforming supplier on the
market. In combination with lightweight molds,
the new RDM 76K (with a forming area of 760 mm
x 530 mm) achieves maximum output while simul-
taneously increasing the service life of the trimming
die. In live demonstrations at the Open House this
resulted in 126,000 PP sealing rim cups per hour on
a 60-cavity mold.
www.illig.de