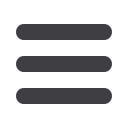
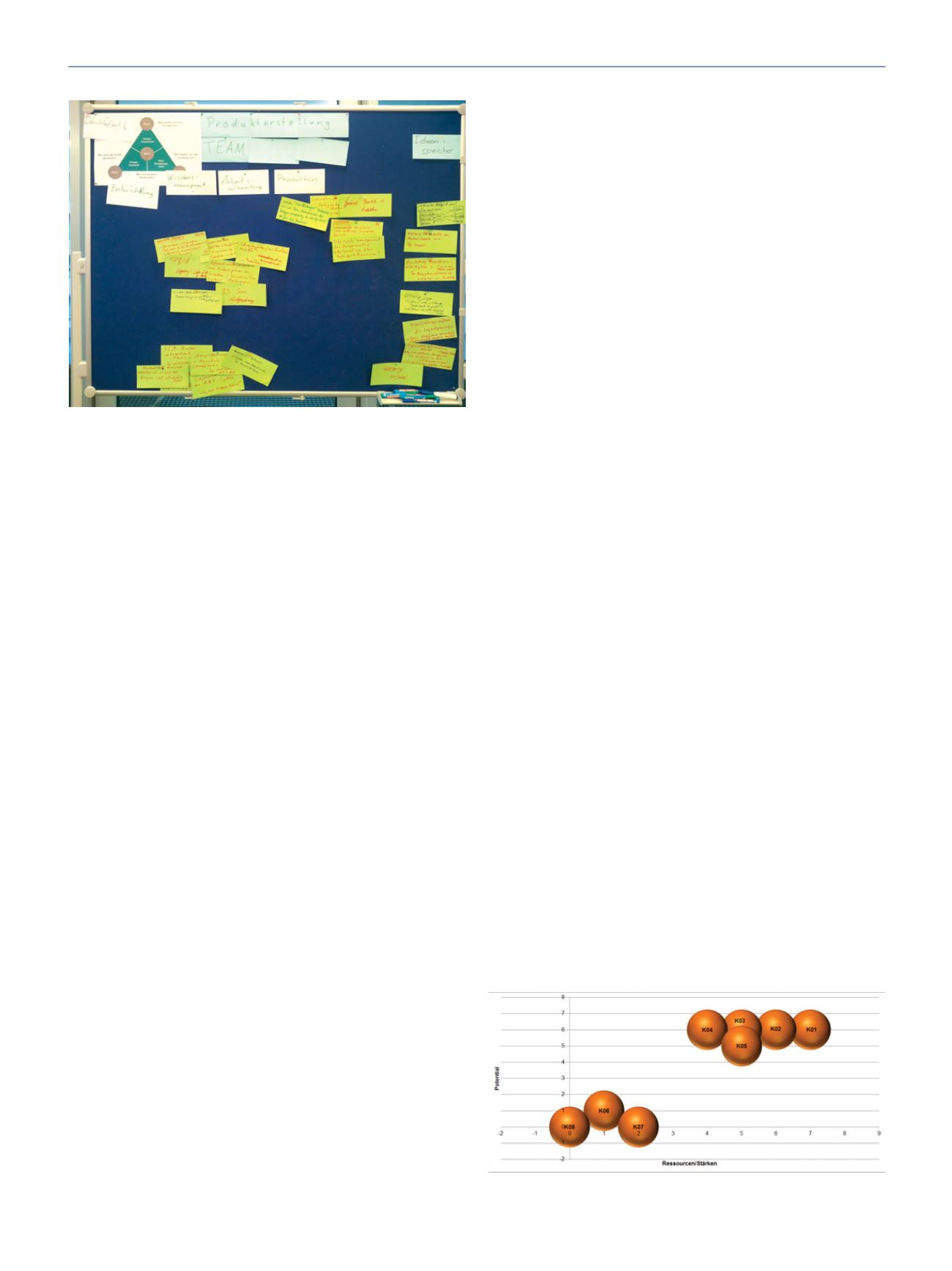
20
Extrusion International 4/2016
COMPOUNDING
determine its optimum operating point depending on the
properties of the raw materials. Similarly, improvements
can be achieved for planning service measures in the sense
of condition monitoring and predictive maintenance, for
instance as a result of changes in differential pressure or an
increase in fine particulates in the clean air.
...but the subject of engineering is being neglected
AZO indeed considers the toolkits to be helpful, even if
“the engineering aspect has not been included” as Her-
zig criticises. “There is very substantial added value spe-
cifically in the engineering for plant design and construc-
tion.” Nevertheless, after thorough preparation with the
help of the toolkits, AZO succeeded in conducting a rigor-
ous analysis of its products. “Once we had classified our
products, we agreed on several important areas where
further development is needed”, explains Bußbach, “but
we didn’t want to tackle all six sections from the toolkit at
once. We wanted to proceed with selected issues in man-
ageable stages. Apart from the criterion for ‘integration
of sensors/actuators’, the plant engineering company
from Osterburken identified connectivity and communi-
cation as a major area where action is particularly neces-
sary. AZO continues to move forward on issues such as
monitoring and data storage, although the company al-
ready considers itself in a good position there with regard
to Industry 4.0.
Until it is possible to further develop products for the pur-
poses of Industry 4.0, creativity will be called for in phase
3 of the Industry 4.0 project. Ultimately it should culmi-
nate in a new product or business model, which requires
ideas to be examined for their market potential, their
benefit and viability – phase 4 of the project. AZO used
the St. Gallen Business Model Navigator recommended in
the VDMA guideline as it examines all these criteria from
every angle. Ideas which promised great market potential
but were assessed as too tight for the existing resources,
were rejected just as were ideas, which, while considered
relatively easy to realise, would however deliver too little
added value for AZO and its customers.
Careful assessment of added value, market potential and
feasibility
Anyone casting a glance at the bulletin board that AZO’s
project team was then using for generating and cluster-
ing, will soon recognise: collaboration with the KIT re-
leased considerable energy: there was no shortage of
ideas. For a mid-sized company in particular however, it
is important to remain focussed in the last phase of the
process, the actual implementation: on issues that are as
high as possible on the right in the matrix for potential
and strengths. Ultimately AZO identified five projects,
four of which are already being actively implemented to-
day. Integrated engineering, pneumatic conveying 4.0,
unambiguous product identification and the screener as
Industry 4.0 component.
Integrated engineering generates added value immedi-
ately in the company itself and has positive knock-on ef-
fects for customers, according to the head of the plastics
engineering division: “Engineering is not only faster and
more affordable; we can also provide the customer with
valuable information in this way.”
Added value from the combination of identification
technology, mobile terminals and information portal
Implementation of the “unambiguous identification”
project also seems relatively straightforward. At AZO this
means it is possible to identify integrated plant compo-
nents at any time and link them with information about
their life cycle. Bußbach clarifies: “When backed by an in-
formation portal, you obtain valuable information about
every component rapidly – whether using QR codes, bar-
codes, RFID or a rating plate.” When were the filters last
changed? Which product is in which receiver at this par-
ticular moment? Which individual parts have been built
in a component – which motor is in the agitator, which
screw feeder in the dosing weigher? It is easy to imag-
ine that the information portal required at a plant engi-
neering company will be extremely complex. Nonetheless
Pic. 3: In workshops ideas are examined for their market potential,
their benefit and viability
Pic. 4: Matrix for potential and strengths to identify
the Industry 4.0 projects AZO will implement