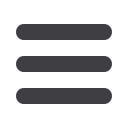
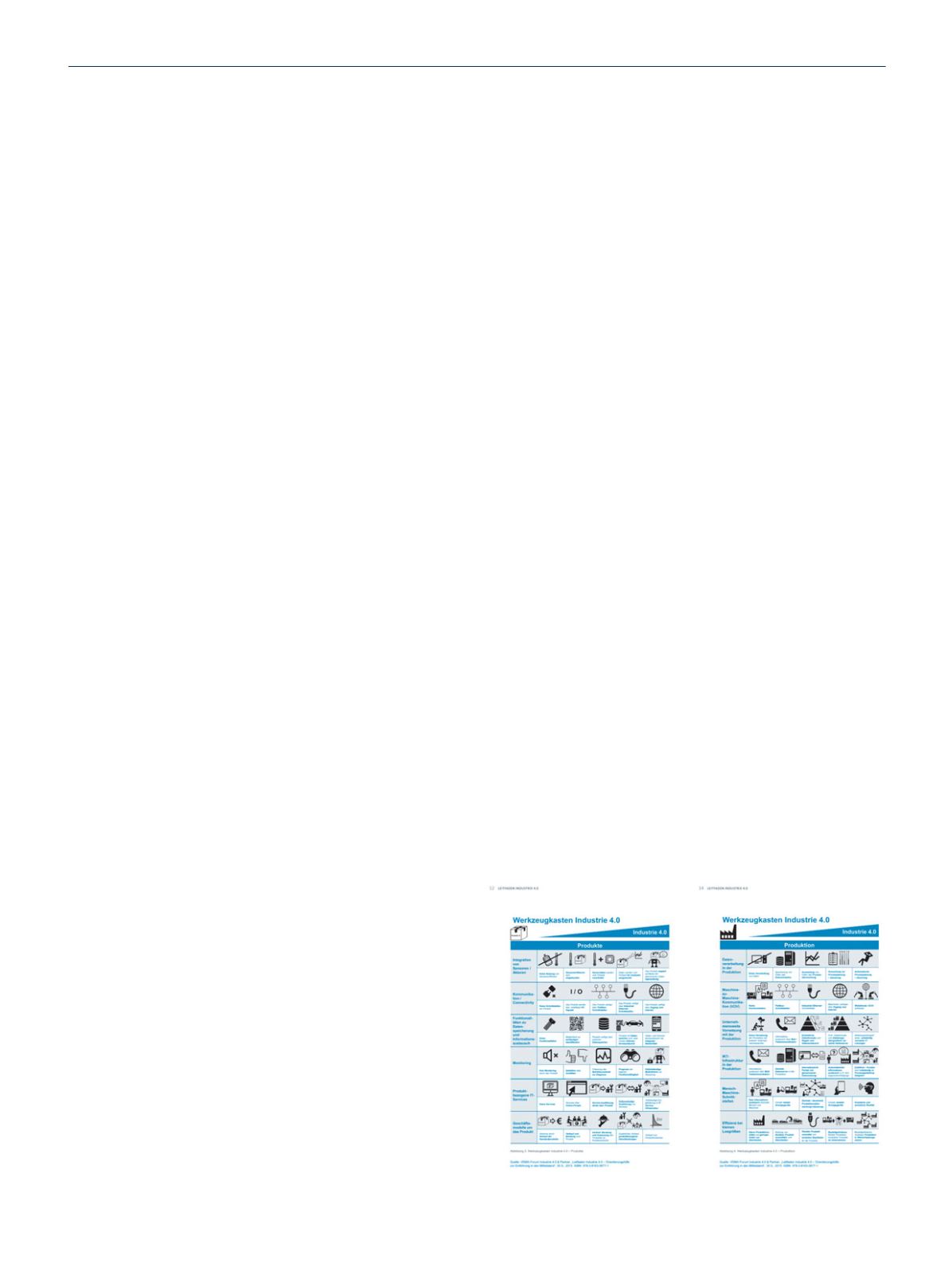
19
Extrusion International 4/2016
things have to be provided from the outset, others can
be “added on” years later without difficulty, as long as
they were included in the planning. And then again other
things may be just “nice to have” – in this case the proper-
ty owner needs to give careful consideration to whether
their available resources allow investment there.
Industry 4.0 and compounding
There is probably an almost unlimited number of “house
pipe dreams” in the plastics industry. And in the com-
pounding sector too, which stands to make huge gains
from connectivity, big data, monitoring and informa-
tion exchange: gains in quality, efficiency and ultimately
increased profit – for businesses and for society. This is
demonstrated by the first projects from the plant engi-
neering company AZO, for example a project in collabo-
ration with Huber+Suhner, a Swiss company specialising
in cable compounds. To achieve its strategy of zero errors,
Huber+Suhner, working with plants and automation en-
gineering from AZO, was already employing methods
in 2011 that come very close to Industry 4.0 in many re-
spects. [evtl. Verweis auf Video
https://www.youtube.com/watch?v=2QNBl3coWu0
Testing Industry 4.0 elements for their efficiency, before
the details for the entire structure have been thrashed
out, is justified. It is equally justified as it would be for a
home owner to first test a modern method of energy sup-
ply in their old home. However that does not save them
the work of giving careful consideration as to how they
want to design their new house with all its features. In
view of the positive experience with Industry 4.0 tools,
AZO management also took a step back in order to ob-
tain a broader perspective of Industry 4.0: What is good
policy? What is feasible – from the aspect of existing re-
sources and capabilities? Which projects should be set up
for it? And what order and priority should be allocated to
the individual projects?
A sound basis – and carefully planned steps
guided by the 4 P
This is how to establish a solid foundation for the future
with Industry 4.0. The ground was well prepared this – a
site with existing infrastructure, as it were. Dieter Herzig,
manager of AZO Controls, underlines: “We have given
some thought to methods such as integrated engineer-
ing or tracking & tracing since back in 2006, issues that
are included in Industry 4.0 today.” The management
was able to build on this when in 2014 they asked: what
does Industry 4.0 mean for AZO and its customers? It was
intended that the VDMA’s (German Federation of Engi-
neers) “Guideline Industry 4.0” for SMEs should provide
guidance for the company’s projects. Karl-Heinz Bußbach,
head of the AZO Poly division, recalls: “We started actual
work on this in early 2015. We first looked for an external
partner to assist us in adopting a newmindset in the com-
pany.” Our chosen partner, KIT, the Karlsruher Institute
of Technology, had already been instrumental in drafting
the VDMA’s guidelines for Industry 4.0. AZO therefore
chose to have input from external experts instead of the
alternative, which was to preside over the entire process
itself with the help of a train-the-trainer measure offered
by the VDMA. Bußbach: “This meant we also gained an
objective view from the experts at KIT.”
Horizontal and vertical integration, end-to-end engineer-
ing and not forgetting the human as director in creat-
ing value are important cornerstones for every business
moving towards Industry 4.0. AZO intends to be guided
– this was the strategic goal decided in the workshop – by
the four Ps: the customers’ production and products and
AZO’s own production and products. Above and beyond
this, the goal is to develop new business models. Bußbach
says: “As digitisation increases, more and more custom-
ers in the plastics industry expect that from us, but so do
customers in other markets.”
Practicable VDMA toolkits...
However before anything can be developed or strategy
rethought, it is essential to know where you stand. AZO
made use of the VDMA’s so-called Industry 4.0 toolkits to
this end. They provide six criteria each with five levels, al-
lowing classification with regard to Industry 4.0, for prod-
ucts and production. For example, the characterisation for
integrated sensor technology: products without any sen-
sor technology were to be attributed to level 1, those with
integrated sensors to level 2, level 3 included products that
themselves process the sensor data, level 4 had products
that also evaluated the data for analyses themselves and
finally products, which respond autonomously as a result
of the data obtained, were attributed to the highest level
5.Definitely important criteria for many of the complex
machinery in AZO’s product portfolio for the plastics indus-
try. For instance, a pneumatic vacuum conveying system,
equipped with additional sensor technology, can itself
Pic. 2: VDMA’s Industry 4.0 toolkits