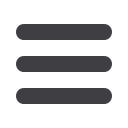
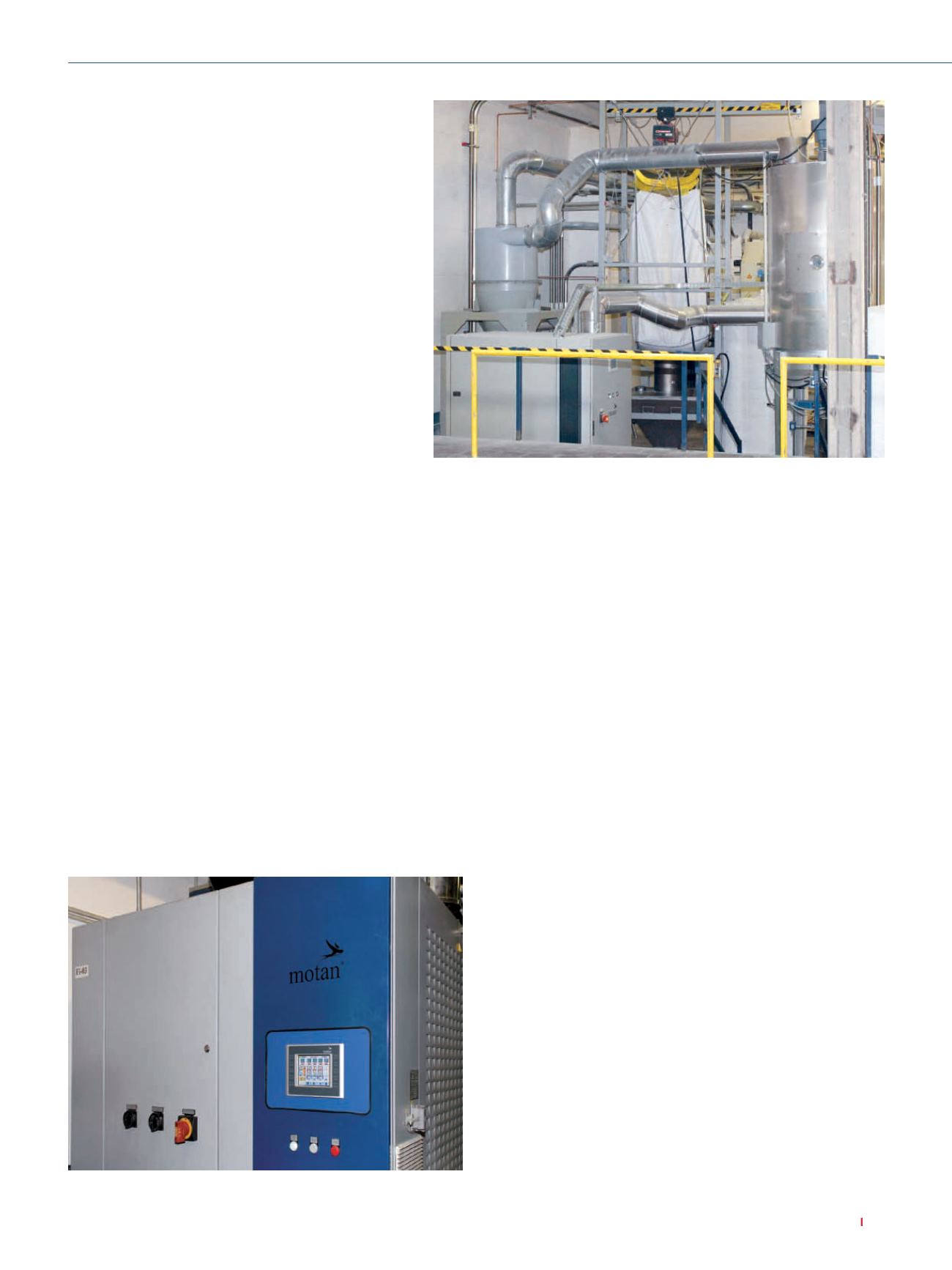
Нидерландах, России, Швеции, Испании, Дании и Таи-
ланде. Успех полиэфирных лент объясняется их много-
численными преимуществами перед обвязочными
лентами из стали. Конечно, по прочности на разрыв
ПЭТ не сравнится со стальными лентами, но для креп-
ления грузов это имеет второстепенное значение. Го-
раздо важнее здесь так называемый ударный резерв, т. е.
способность поглощать импульсные нагрузки. К этому
следует добавить эластичность, компенсирующую по-
тери натяжения при обращении с грузами, подвержен-
ными усадке. У лент Cyklop она достигает 14 % в
зависимости от исполнения. У стальных лент эластич-
ность составляет не более 1 %. Кроме того, ПЭТ не ржавеет,
опасность травм при его использовании заметно снижается, он
не повреждает даже чувствительные грузы, и, конечно, ПЭТ го-
раздо легче стали. Преимуществом ПЭТ перед полипропиле-
новыми обвязочными лентами является температура
стеклования 60-70 °C, благодаря чему грузы надежно удержи-
ваются даже в жару.
Просто только на первый взгляд
На заводе Cyklop в Кёльне, оснащенном экструзионными ли-
ниями и необходимым периферийным оборудованием, изгота-
вливается около 50 разных видов обвязочных ПЭТ лент,
прочность на разрыв которых составляет 2000-13000 Н в зави-
симости от поперечного сечения.
ХРАНЕНИЕ, ПОДАЧА И ПОДГОТОВКА МАТЕРИАЛОВ
Экструзионные линии имеют до 10 отдельных ручьев, их общая
длина со всей периферией составляет 90-100 м. После выхода
из экструзионной головки ленты сначала охлаждаются в водя-
ной ванне, после чего вытягиваются в два раза на последующем
оборудовании. Затем они проходят через станцию тиснения, к
которой примыкает печь, где устраняется напряжение мате-
риала. Затем следуют участок охлаждения, печатающее устрой-
ство для нанесения надписей или маркировки, а также
намоточная станция, где пленка готовится к последующей от-
правке. Конструкция экструзионных линий предусматривает
почти полное резервирование, в том числе и последующего пе-
риферийного оборудования. Это означает, что при отказе од-
ного из компонентов, например смесителя, выполняется
автоматическое переключение на другую станцию смешивания
без остановки производственного процесса.
Производство ведется в круглосуточном режиме семь дней в
неделю. На первый взгляд все просто, но на деле это очень
сложный процесс, особенно в том, что касается обращения с ма-
териалами. Характеристики необходимого здесь оборудования
должны соответствовать показателям производительности экс-
трузионных линий, а это 450-600 кг/ч.
ПЭТ — непростой материал
В начале своей «карьеры» в качестве материала для изготовле-
ния обвязочных лент ПЭТ считался технической пластмассой,
и, соответственно, стоил дорого. Только в начале 90-х гг., когда
на европейском рынке появились бутылочные ПЭТ хлопья, он
перешел в разряд пластмасс массового применения. «Пред-
приятия по утилизации и вторичной переработке внезапно
обеспечили нас достаточным количеством вторичного мате-
риала, это помогло решить проблему высокой стоимости новых
материалов», — вспоминает Бернд Кауземан, генеральный ди-
ректор предприятия. «Тогда речь шла прежде всего о реграну-
ляте, потому что хлопья, как правило, были сильно загрязнены.
В середине 90-х гг. нам впервые удалось использовать буты-
лочный регранулят для изготовления полиэстеровых лент», —
В уже имеющуюся инфраструктуру был интегрирован
кристаллизатор Luxor HDC 1800, оснащенный
бункером с мешалкой вместимостью 2500 л,
с загрузчиком для хлопьев Metro HCG 30 MG
Система управления для сушилок Luxor-Net, в серийном
исполнении оборудованная гибкой шиной, позволяет
установить до 16 сушильных бункеров и до 24 загрузочных
устройств. Наряду со средствами регулирования и контроля,
в офисе начальника смены предусмотрена централизованная
станция, дающая доступ ко всем данным
ЭКСТРУЗИЯ
2/2016
45