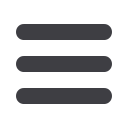
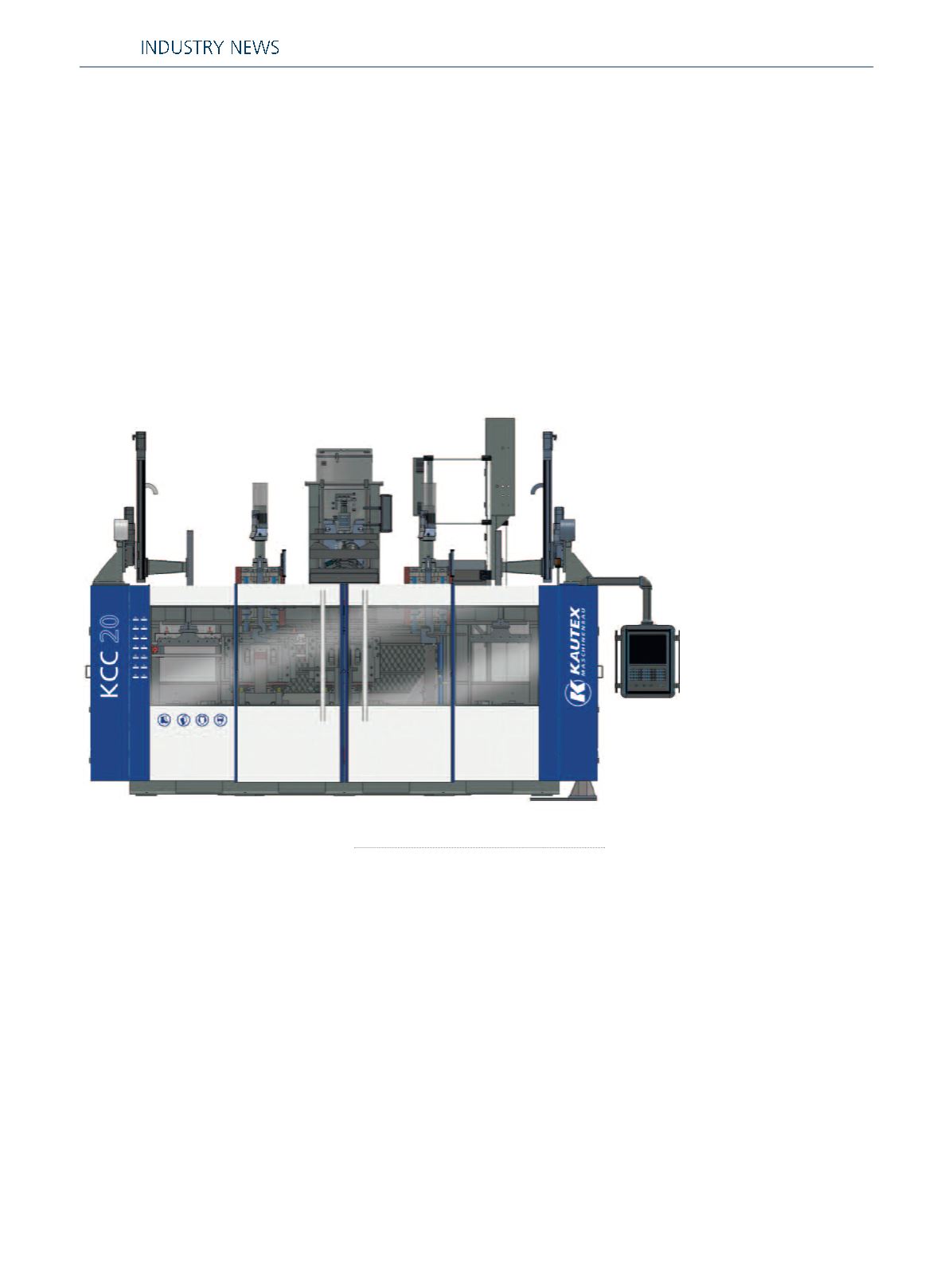
Extrusion International 2/2016
18
At this year’s Chinaplas, which will be held in Shanghai from
25 to 28 April 2016, Kautex Maschinenbau will present a new
model in its successful KCC series of extrusion blow molding
machines. This is the third generation of the KCC series, which
has been produced in Shunde, China, since 1997.
The new blow molding machine model, which was announced
at the Open House event in October last year, represents a com-
plete relaunch of the KCC series. As well as a number of new
and revised technical features, the machine has also been com-
pletely re-designed, to visually blend in with the look of new
Kautex machines.
Third generation of KCC machines go into production
www.kautex-group.comWith its compact form, the new KCC generation takes up less
floor space in the production hall. Better accessibility not only
makes the blow molding machine easier to service, but also
speeds change over times. Molds can now also be changed from
the side, for example, and products are discharged from the rear
of the machine. A greater standardization of modules and com-
ponents has reduced the investment costs of the new machine
and shortened future delivery times.
New KSB suction blow molding machine
Kautex Maschinenbau will also allow first insights in its new KSB
suction blow molding ma-
chine at Chinaplas. This
brand new machine type
was specially designed for
low-flash production of 3D
molded parts. Global de-
mand for plastic ducts for the
automotive sector is rising all
the time, ever since the use
of special materials such as
PA6.6 or PPS has enabled the
production of highly heat-re-
sistant exhaust ducts.
A modern operating concept
with Kautex BC5 controller
makes the new KSB machi-
nes easy to operate. In addi-
tion, the new suction blow
molding machine takes up
almost 50% less space than
previous equipment, thus re-
ducing investment costs.
Tailored LFT compounds the reliable way
ProTec Polymer Processing's focus at this year's Chinaplas from
25 – 28 April in Shanghai will be on the production of long-fibre-
reinforced thermoplastics (LFT) by pultrusion and on the new ge-
neration of ProTec tumble reactors. These SSP (solid-state
post-condensation) reactors are ideally suited to improving the pro-
perties of flowable plastics. Examples include the post-condensa-
tion of pelletised polyesters (PET, PBT, PEN etc.) and nylons such as
PA6 and PA6.6. These "upgraded" materials are then for example
converted into bottles, fibres and industrial yarns which are requi-
red for optical waveguides, tyre cords and for airbags, fibre-com-
posite materials, filter fabrics or nonwovens. When injection
moulded, LFT compounds with fibre reinforcement along the
length of the pellets result in components which combine high
strength and light weight with very good surface quality. LFTs with
a fibre length of around 12 mm are ideal for further processing.
Flexible, versatile LFT technology
ProTec's LFT technology is suitable for producing a wide range of
materials with differing levels of fibre reinforcement and many dif-
ferent polymer matrix materials which may also be directly com-
pounded during LFT manufacture. Even the difficult pairing of
carbon fibres with PP can be reliably processed. ProTec's head-
quarters in Bensheim (Germany) has a versatile cutting edge pul-
trusion line for application-specific customer testing and basic