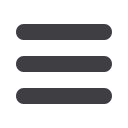
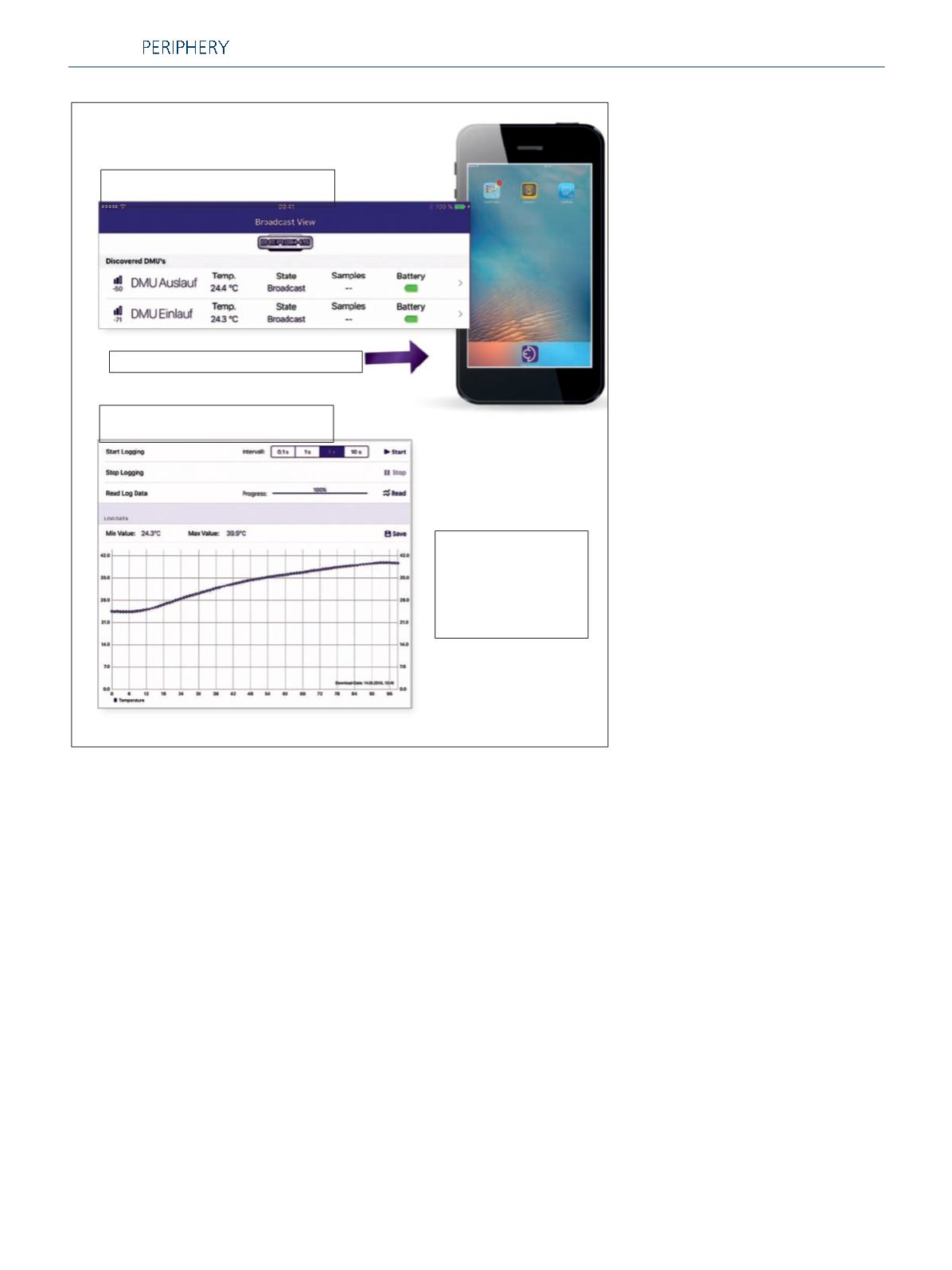
machines and makes them fit for use. They determine and
interpret data from their physical environment via sensors.
They are capable of gathering, digitalizing and wirelessly (at
least over a short distance) transferring data to a central pro-
cess computer and thus easily to the Internet. With the help
of so-called actors, they can influence physical processes in
their environment, prevent production down-times, minimize
material and energy consumption and help the operating
personnel with intervention and prevention. With this multi-
modal human-machine interfaces, production requires fewer
resources and is more energy efficient.
DERICHS ED1 – Temperature, pressure and flow rate control:
With the DERICHS ED1, Derichs is taking a huge step in ex-
actly this direction. This tool provides every roller with a digi-
tal memory. It can be retrofitted on any double-shell roller
and can data such as inlet and outlet temperature and input
and output pressure and the resulting profiles of each indivi-
dual roller can be displayed. Transferred wirelessly via wireless
radio to an app developed for Android or Apple systems, the
DERICH ED1 allows for direct and extremely precise monito-
ring of the actual values. This results in
new, additional options for the process
technicians to monitor and influence
the extrusion process. What is also in-
teresting for the machine manufactu-
rers is the possibility of directly
integrating the interface into the system
electronics. By means of regular, auto-
nomous screenings, the roller itself can
provide feedback if a significant change
in the internal conditions occurs. It is
therefore possible to intervene in the
overall process earlier and faster. In ad-
dition to optimizing the film, focus is
placed on the maintenance and re-
source conservation of the operating
medium and the roller. With respect to
further development, it is possible that
recommendations originating from the
roller regarding interventions in the on-
going process may be used in a variety
of ways for optimization. We can’t even
currently conceive the potential diversity
of options.
The development:
After initial feasibility studies by Profes-
sor Peter Gruber from the University of
Basel, the DERICHS ED1 was developed by the team sur-
rounding Professor Roland Keung in cooperation with the Zü-
rich University of Applied Sciences (ZHAW – Zürcher
Hochschule für angewandte Wissenschaft, School of Engi-
neering, ZSN) and has already been successfully tested on a
roller in a laboratory. Professor Roland Kueng from the Uni-
versity of Zürch is very convinced of the benefits for the cus-
tomers: “With this new Derichs development, the
temperature, for instance, can be precisely monitored during
production. First, because the measurement is taken directly
in the roller coolant and second, because the value is digi-
tally available to the heating controller as an actual value. If
the water temperature in the roller is reduced by 1%, this
saves 6% energy. If, for instance, there are greater deviati-
ons, an alarm can be triggered and the system can protect it-
self from being damaged.”
The facts:
The fact that the measurement values are digitalized directly
at the sensor by a measuring electronics system and a mi-
croprocessor offers the benefit that they are very precise and
The new innovation from Derichs:
the 1st electronic measuring tool for
monitoring the temperature, pressure
and flow rate in the roller
Permanent monitoring
Logging
Temperature curve
over a self-determined
logging period
...Control also via DERICHS App
Extrusion International 5/2016
36